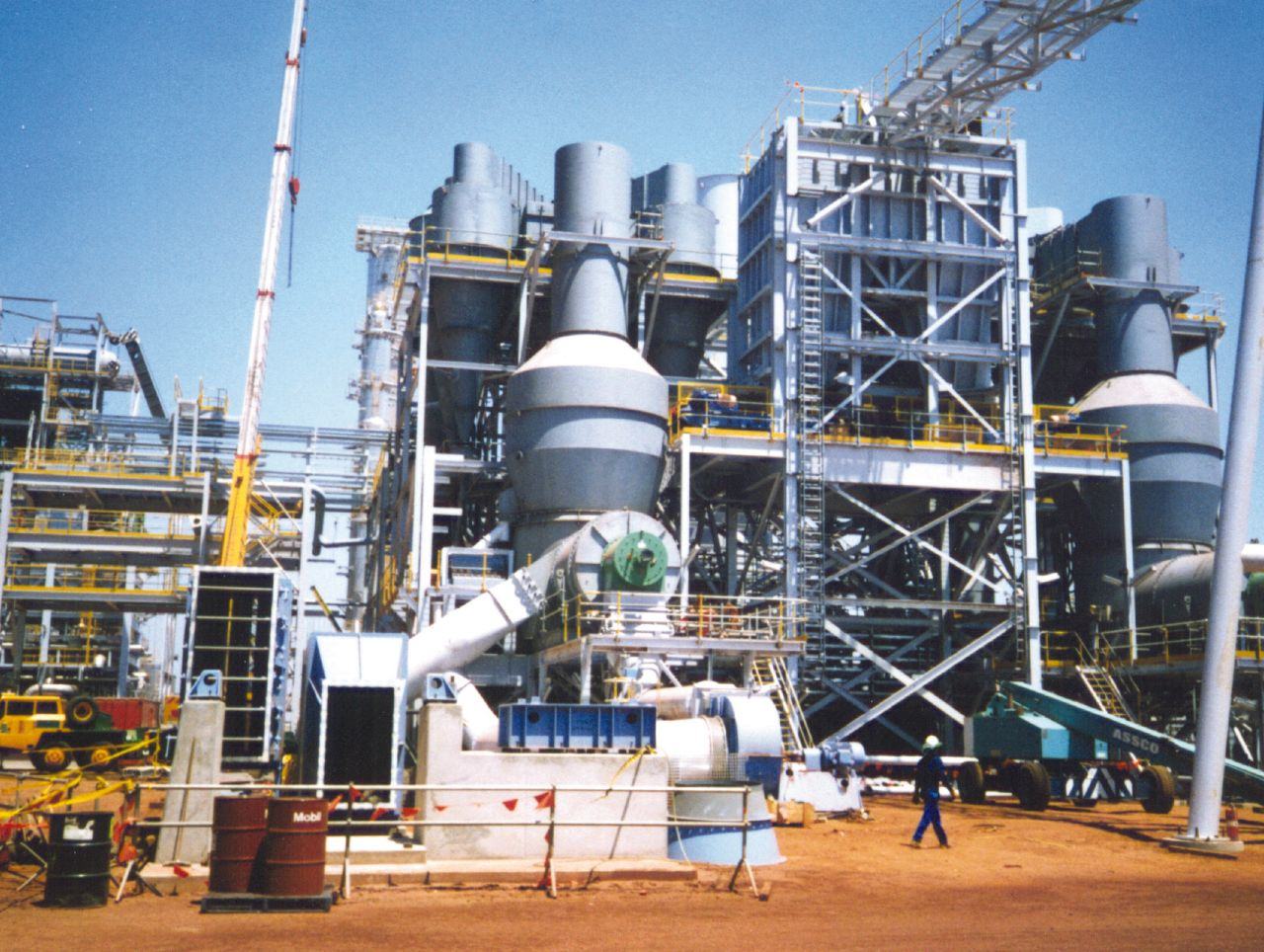
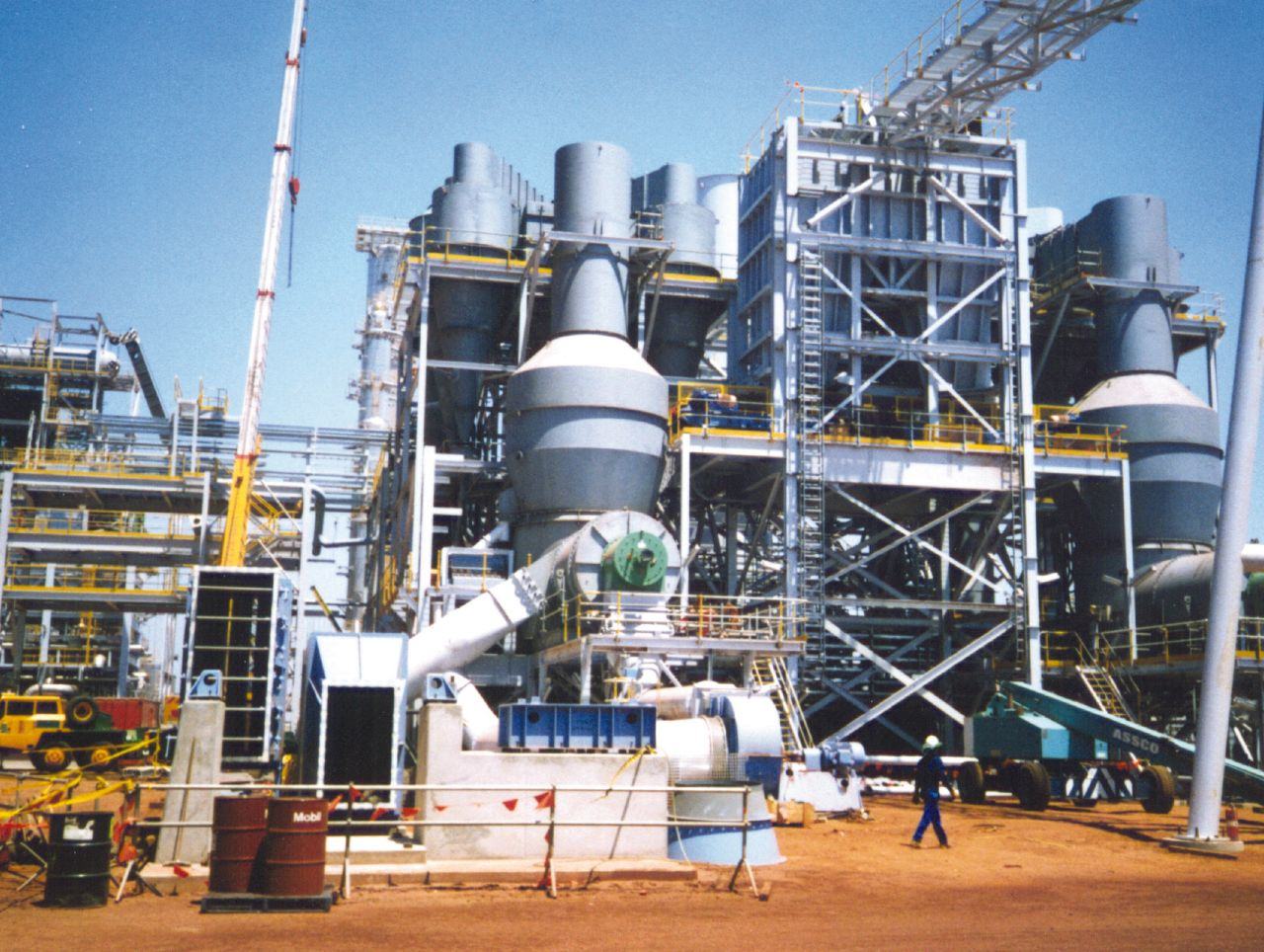
Supporting your operations, from plant design expertise to equipment, parts and services for every stage of your process.
Are you looking to increase production, reduce risks, lower operating costs and enhance environmental performance? Then you are in the right place.
From the design and supply of products for a greenfield plant, to the addition of a single machine for an existing production line, we are here to help.
Rely on OEM experts because not all parts are created equal. Spare and wear parts built to perform.
Helping you get the most out of your equipment and processes.
Metso has over 30 years of fluidized bed history and has over 200 systems installed under the Pyrotherm, Svedala, and Allis Chalmers brands. Metso fluid bed technology has a proven track record of excellence and has a lower CAPEX and OPEX versus other cooling, drying, heating, and calcining technologies.
High throughput rates – up to 600 tph
High rates of heat exchange
Does not overheat individual particles
High levels of intermixing of the particles
Is suited for powders, granules, agglomerates, and pellets 50- 5,000 micron
High energy efficiency
Mechanical simplicity
Continuous operation
Low maintenance (no moving parts)
System is automatic and does not require constant operator presence.
The fluid bed technology is applicable in a multitude of industries and minerals processing such as mineral sands (ilmenite,rutile, zircon, leucoxene, garnet) iron ore drying, diatomaceous earth, phosphates & potash, lithium spodumene, lime and various other industries.
Fluid bed technology can be for stand-alone units or complete systems deliveries including PLC control, dust/product collection, product conveying (feed and discharge), exhaust gas handling, heat exchanging, and fuel delivery systems.
The introduction of an appropriate air flow into the system brings about the onset of fluidization. The air flow passes through the bed of material and suspends the particles in a fluid state. The bed has the appearance of a vigorously boiling liquid, and will flow steadily through the vessel from one side to the other and discharge over a set weir plate or bed level control feeder. Each particle is suspended by its own pocket of gas maximizing the heat transfer rate. This results in an extremely efficient heat transfer process.
Applicable industries:
Mineral and coal applications
Iron ore
Plastic and polymer
Limestone
Potash & phosphate industries
Rare earth elements