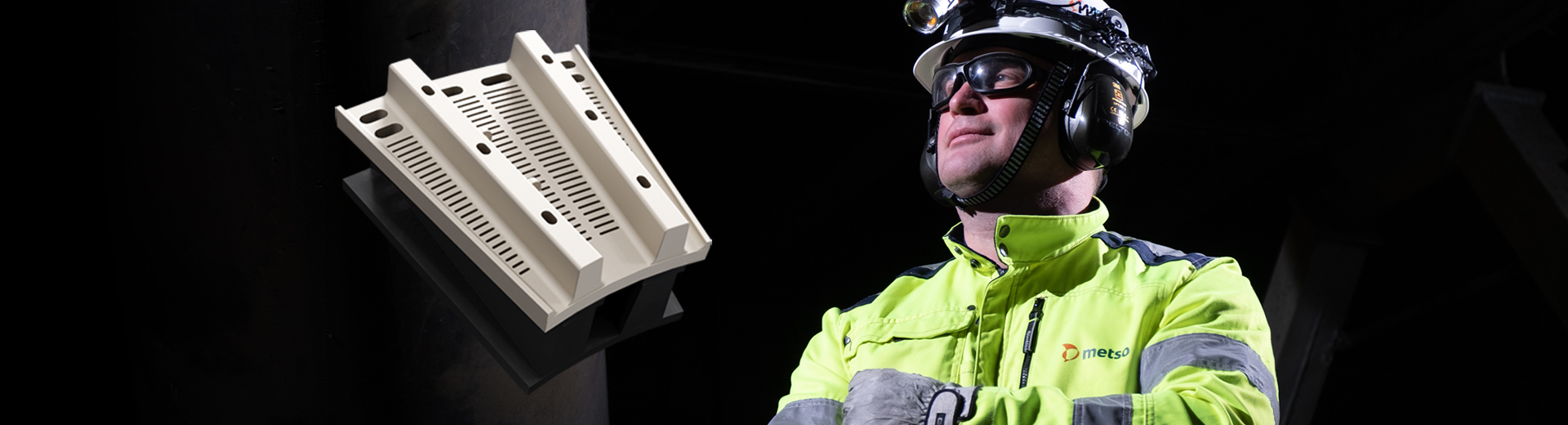
Benefits
No workers needed in the danger-zone inside the mill
Up to 50% faster relines
Up to 70% fewer parts
High-performing parts improve efficiency, and long-lasting parts mean fewer parts are needed

Fewer parts mean up to 50% faster change-outs
The discharge system of a mill is the most complex and time-consuming part of the mill to reline.
The new Megaliner™ for discharge systems integrates dischargers, grates, lifter bars and filling segments in one unit, reducing the number of components used by as much as up to 70%. This can cut your installation time in half.
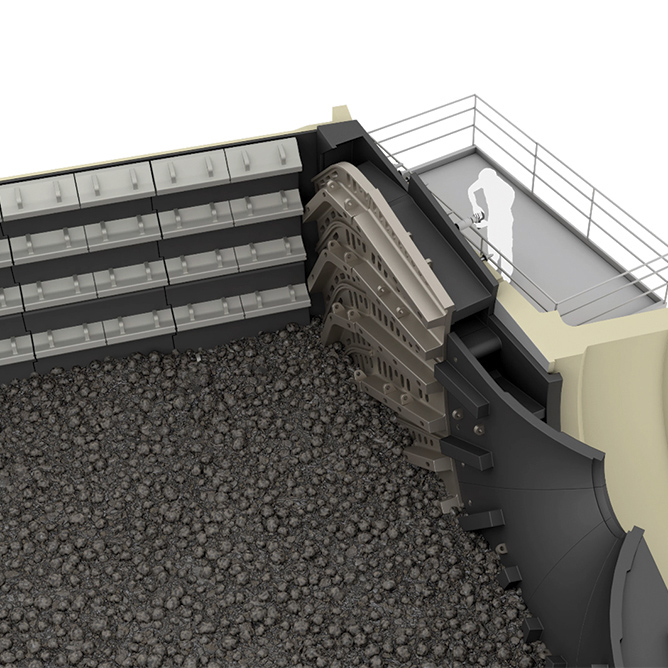
The ready-made modules have a minimized number of attachment points and the bolts used to attach the liners are inserted from the outside of the mill, meaning that no workers are needed in the danger-zone inside the mill. The work can instead be performed on steady and safe platforms.
The liner bolts are much shorter and well protected from dust, corrosion and general mechanical damage, making them longer lasting and easier to remove. The traditional long bolts through the grate, the pulp lifter and the mill discharge head are not used, making it up to 70% faster to knock out the bolts. It also eliminates the need for risky and expensive recoilless hammers.
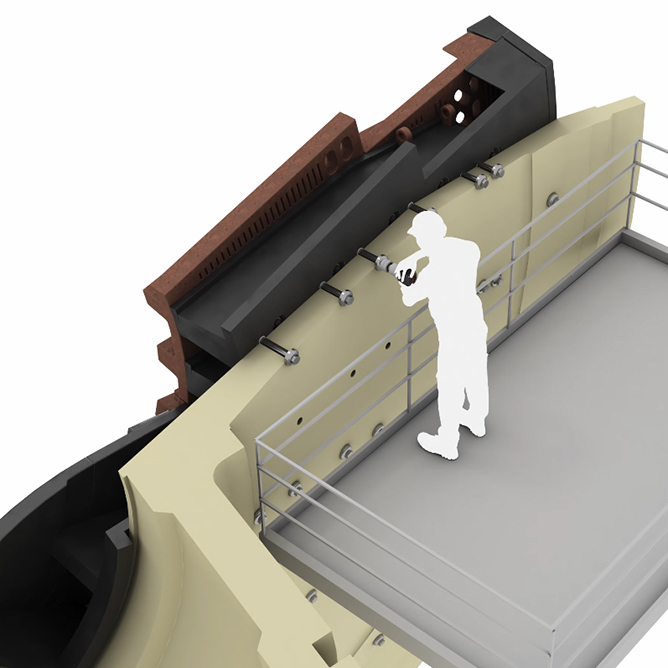
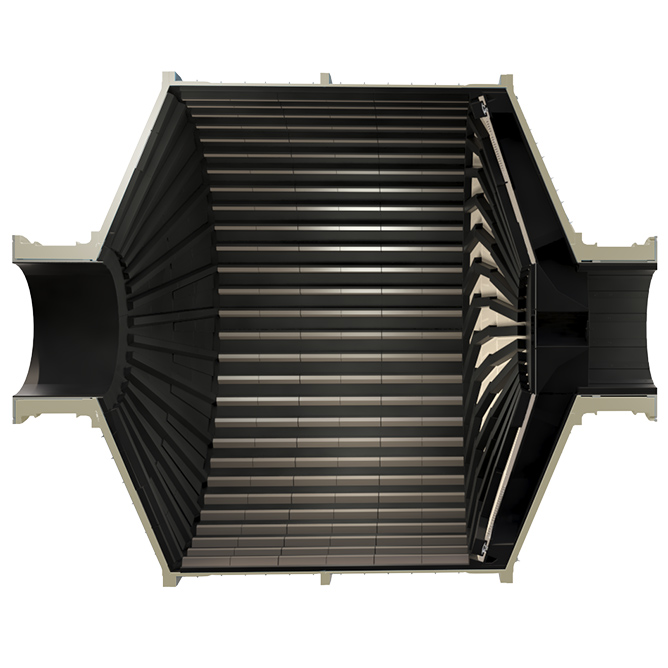
With this latest innovation, Megaliner™ is now available for all sections of horizontal mills: the head, the shell and the discharge system.