Solutions for reducing emissions and increasing energy efficiency

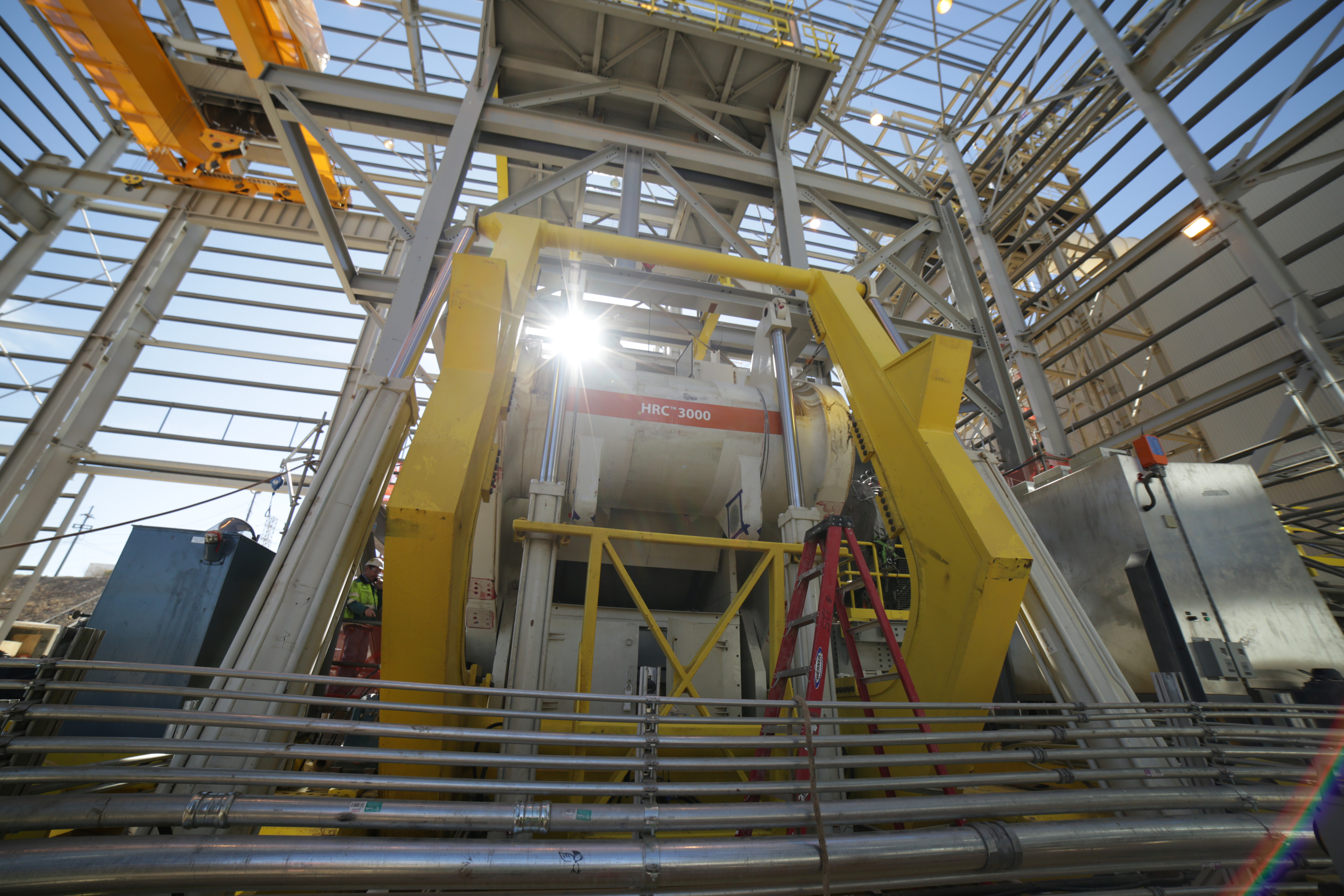
Solutions for energy and emissions efficiency
More efficient and sustainable solutions in minerals processing are essential, as our customers must satisfy the growing demand for minerals while battling against reducing ore grades and tighter sustainability requirements. Our products offer energy-efficient options for e.g. material transport, size reduction, mineral separation and dewatering.
Metso’s comminution portfolio includes products such as the HRC™ high pressure grinding roll (HPGR), the Vertimill® and the HIGmill™ which all directly reduce the amount of energy required in comminution.
Primary grinding in the HRC™ HPGR can reduce comminution energy requirements by up to 30% compared to a conventional mill. Similarly, Vertimills® and HIGmills™ have been shown to save 35% or more on fine grinding energy. Emerging technologies, like ore sorting and early rejection of waste materials, can also reduce energy intensity through their ability to reduce the amount of ore that needs to be processed for a given amount of final product.
In aggregates, the biggest potential for reducing emissions lies in moving to electric equipment. Around 45% of our aggregates product portfolio is already electric.
Our extensive portfolio
Our comminution portfolio also has positive impacts on the indirect, or embodied, emissions created by our customer’s operations. Grinding media is a perfect example of embodied emissions. Vertimills® typically consume 20% less media than an equivalent ball mill, and approximately one half the grinding media compared to a ball mill.
In addition to comminution, there are other areas where our portfolio improves the energy efficiency of our customer’s operations. FloatForce, for example, is a novel impeller mechanism available as a retro-fit in large flotation tanks cells. A key additional benefit of this technology is improved metallurgical performance. Improved recovery in flotation means that more concentrate can be produced per tonne of ore, thereby significantly reducing energy intensity per tonne.
In 2024, we made EUR 8 million investment in a direct reduced iron (DRI) Smelting Furnace pilot facility in Pori, Finland. This facility aims to test, develop and validate the technology further with customers, demonstrating the applicability and results of industrial-scale DRI smelting. The new processing route can replace traditional blast furnaces used in iron and steel making, which generate most of the CO2 emissions in steel production. This is an optimal solution for primary steel producers aiming for a significant reduction in their CO2 emissions with minimal changes to the rest of the steel plant.
Metso also leverages Advanced Process Control (APC) to reduce our customer’s energy needs. APC comprises of sensors and regulatory control systems that can pro-actively optimize the operation of various parts of a concentrator. Similarly, camera-based sensors are used to evaluate the formation and transport of froth in flotation cells. Changes in air flow and reagent dosage automatically adjusts to optimize recovery, which can lead to substantial energy savings and greater profits for our customers.
In 2024, we launched Metso’s first diesel-electric Lokotrack EC range units. All process functions are electric, significantly reducing the use of hydraulic oil needed in crushing operations. This new Lokotrack® transformational technology will support our crushing and screening customers by providing easy-to-use diesel-electric equipment that can be run from an integrated Genset or connected to an external power source. This results in lower operational costs and allows access to renewable energy sources.
