The new Skega™ Life rubber compound is developed in our own laboratory and validated by field studies. To learn more about this new rubber, let’s ask our mill lining experts, Fredrik Johansson, Global Product Manager, Rubber and Poly-Met, Mill Lining and Lars Furtenbach, Director, Research & Technology Development, Mill Lining.
Stretching the life of your mill liners
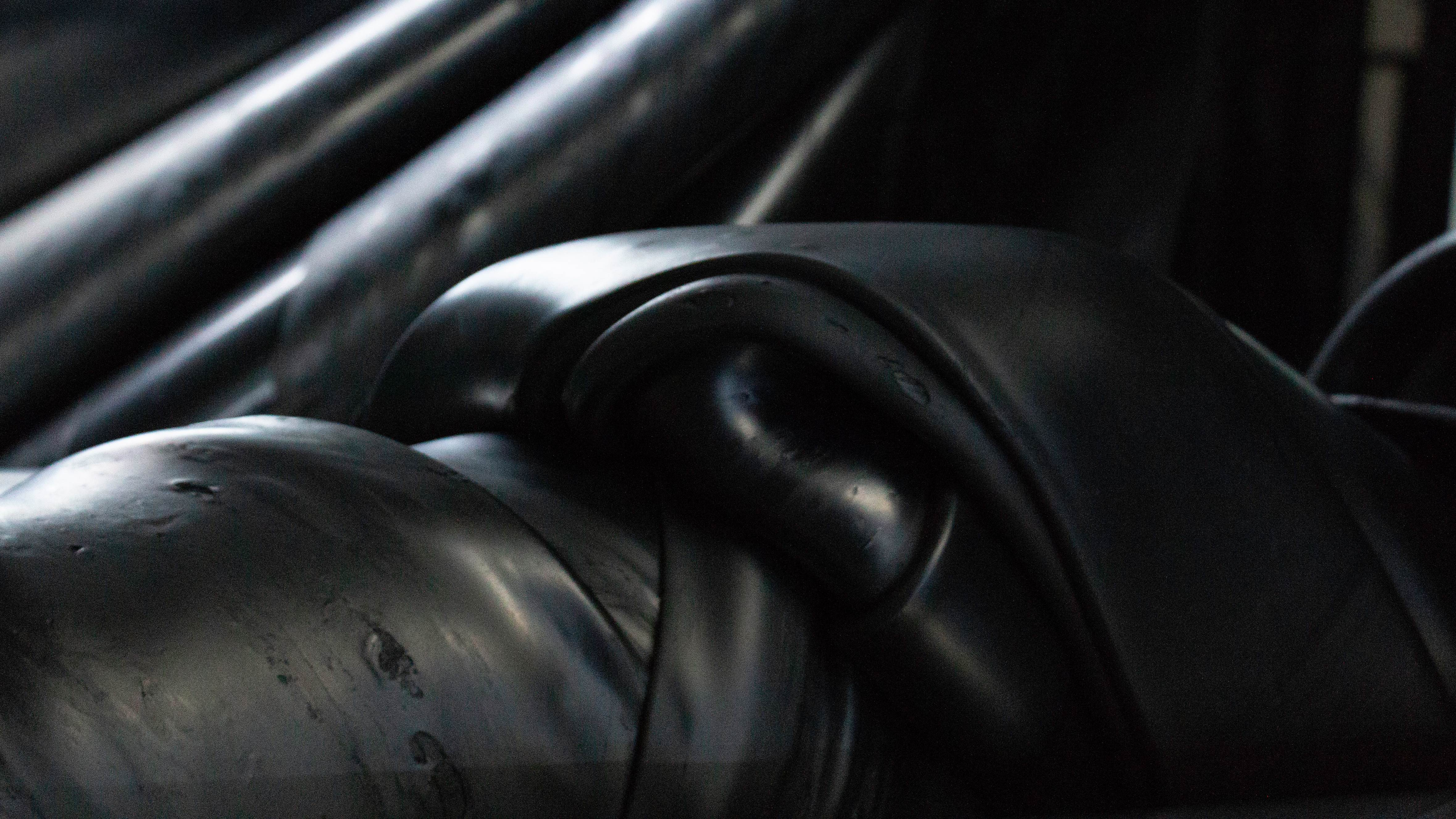
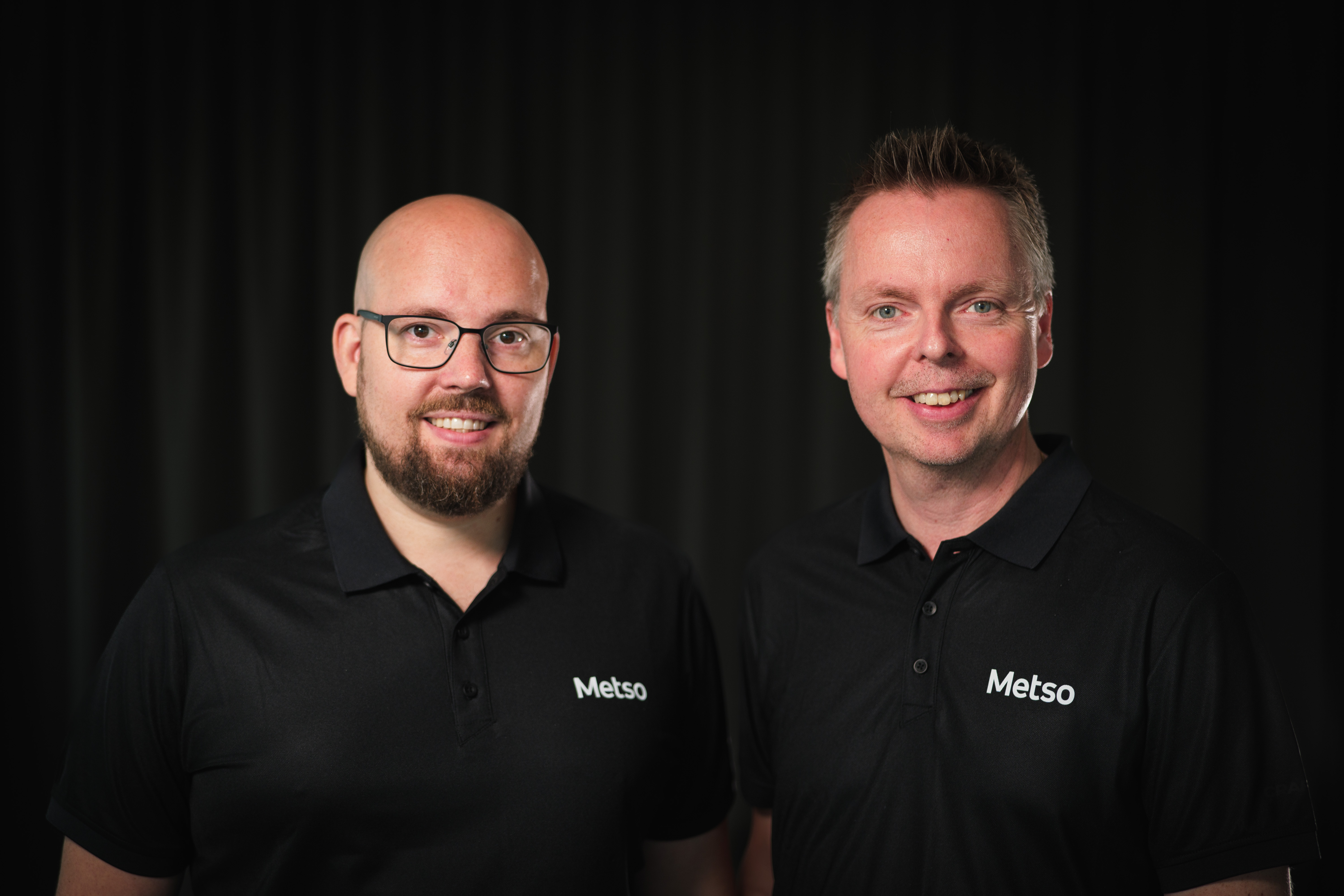
What are the main benefits of using rubber in mill liners?
“Grinding is a tough process, especially when grinding abrasive ores, and the mill liners play a crucial role. Rubber has the benefits of low weight, no leakage or peening and it also reduces the noise level around the mill. Due to the lighter weight, the change-out is easier and safer. Rubber can also be combined with other materials for even better result. By combining materials, you can use each material where it performs best to optimize your grinding process and make it more sustainable” says Fredrik Johansson.
“Mill liners from Metso are so much more than just wear parts. Our mill liners are never made in a “one size fits all”, they are designed by our experts to meet the customers’ specific targets and operating conditions” he continues.
Skega™ Life rubber was recently introduced; can you describe what it is and what the main benefits are?
“Customers are facing many different challenges depending on their situation and targets. This new rubber compound is especially developed to have properties of longer wear life compared to our current premium rubber Skega™ Classic. Up to 25% longer wear life will help our customers to reach many of their safety, sustainability and performance targets. The longer wear life will give you increased uptime between the stops and this is especially important if you have other wear parts that you need to match the wear life of. Longer wear life also means fewer maintenance stops and therefore less time in hazardous areas” says Fredrik Johansson.
Sustainability is a hot topic in mining these days. Does Skega™ Life have any environmental benefits?
“Skega™ Life is part of Metso’s Planet Positive offering of products that bring environmental advantages. Extending the life of your mill liners results in less CO2 emissions in the overall value chain due to reduced use of materials as well as less transportation. Furthermore, we have not used any harmful high aromatic (HA) oils in our rubber since year 2000” says Fredrik Johansson.
What have been the results from field studies?
Metso is working continuously to develop new compounds, with the main objective to produce more sustainable and high-performing rubber compounds. Since 1959, we have been in the forefront of developing new rubber solutions for mills around the world. With this new rubber, we are taking the next step in rubber performance.
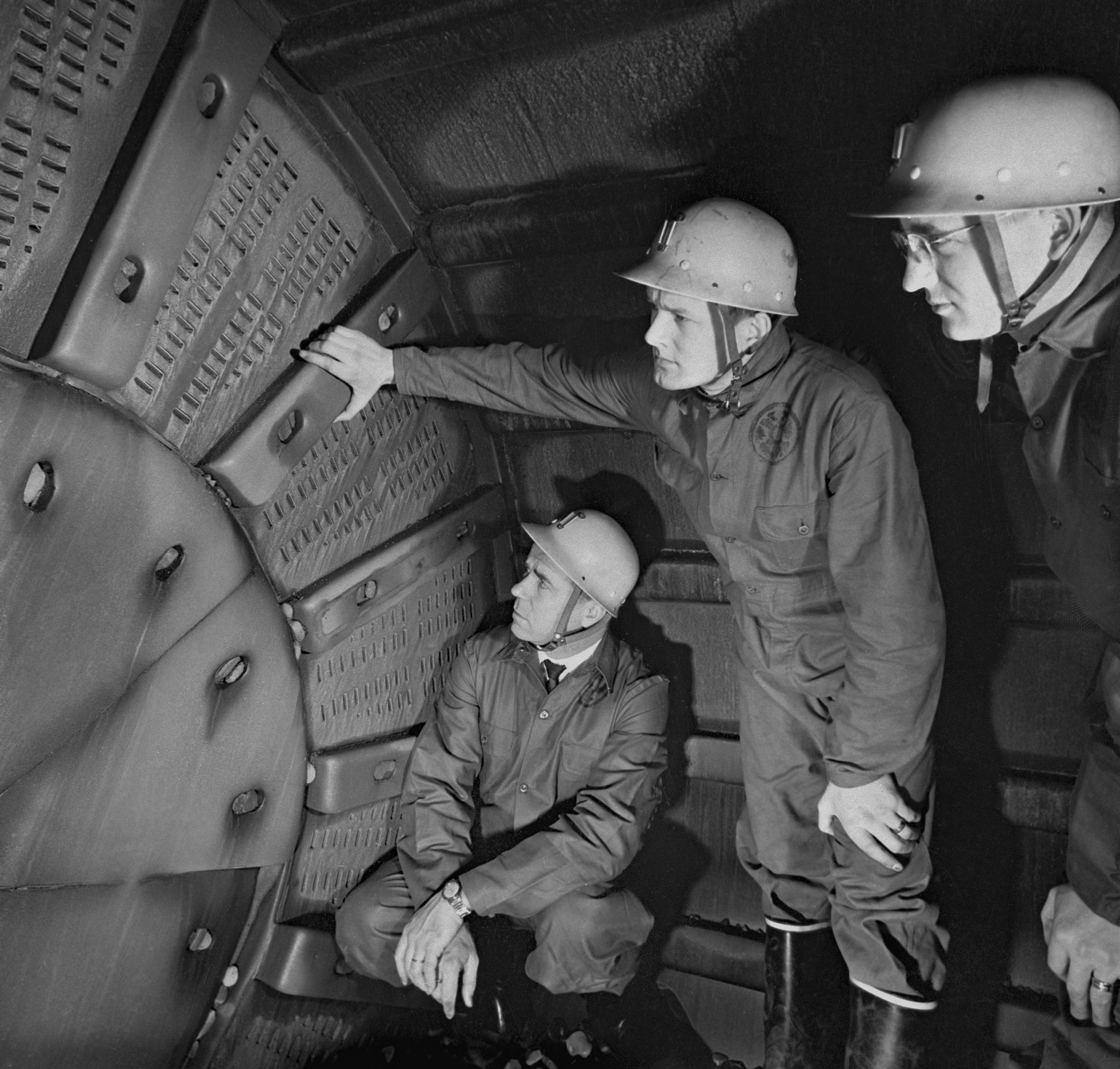
One of Metso’s labs are situated in Skellefteå, northern Sweden, where Lars Furtenbach and his team, together with other material experts, are conducting tests, trials and developing new rubber compounds.
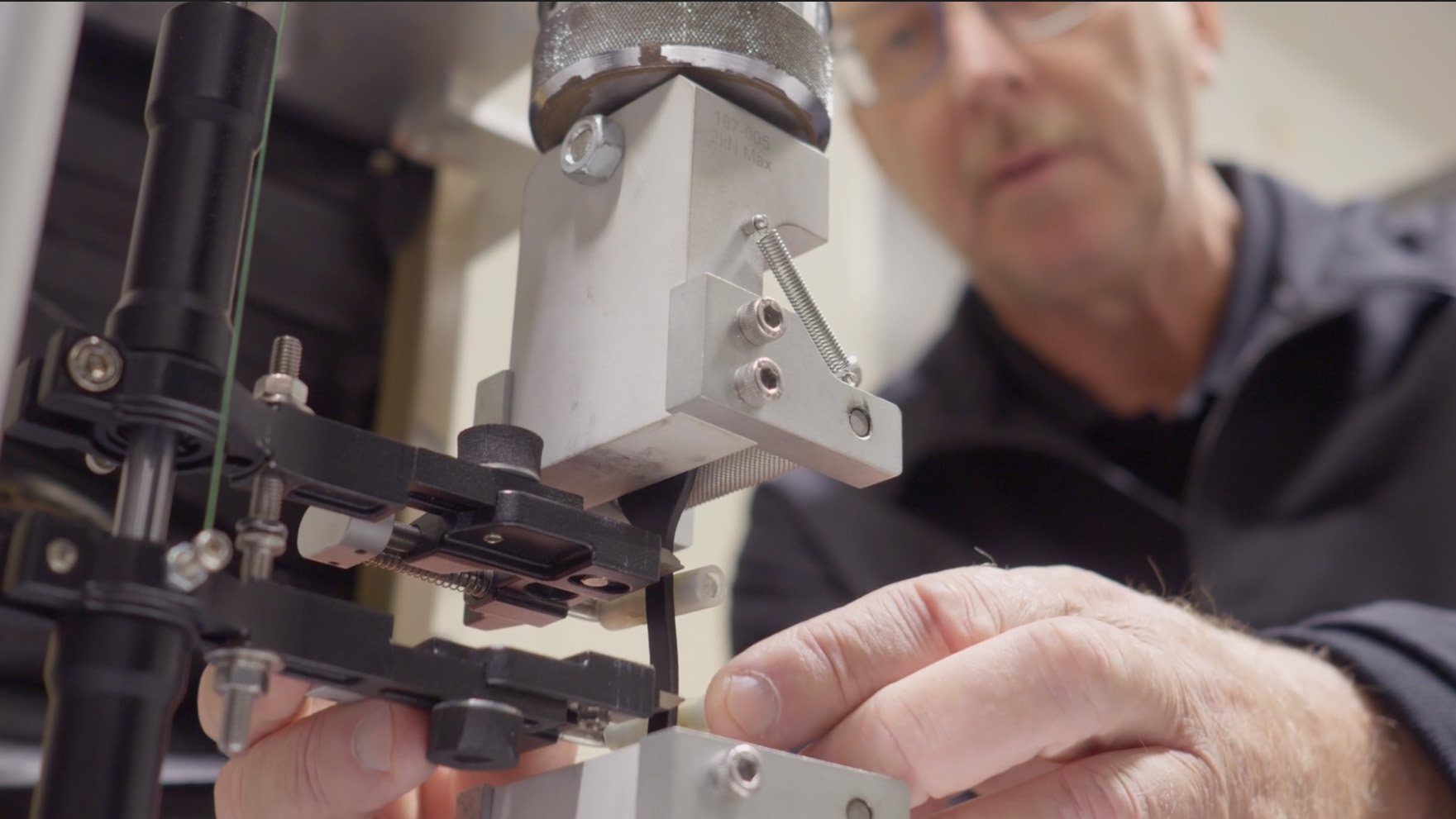
The new Skega™ Life compound was developed in this lab, and it has been validated by several tests and field studies. When conducting the trials, we have compared the results to our current premium rubber, Skega™ Classic.
"This rubber needs to endure abrasion, the tumbling of rocks, and other extremely demanding forces over extended periods. Developing material that can withstand such conditions is a complex process. The results we are observing now are beyond my wildest dreams. It makes me proud and delighted that we are achieving such success and harnessing such profound expertise.” says Lars Furtenbach.
“This new rubber will have improved wear resistance and give a value to the customer of increased sustainability, safety and production through optimized throughput and increased uptime, all due to the longer wear life” he adds.
When will it be most beneficial to use Skega™ Life rubber?
"This new rubber will be most beneficial to use when the customer wants to reach targets concerning sustainability, safety, lower maintenance and longer uptime.
This rubber can be used in any rubber application, but most suitable in ball mills larger than 14 feet, AG and SAG mills of 18 feet or smaller. The rubber is specially developed to have very good wear resistance in grinding mills processing high abrasive ores", says Fredrik Johansson.
