“During the first year, we were extremely successful at processing our entire annual throughput using the GP330. Everything worked well and our requirements regarding the end product quality and capacity were fulfilled. Thanks to the IC50C automation system, all the functions of the crusher can be easily adjusted, which is a clear improvement over its predecessor from the 1980s. To secure trouble-free operation for the future as well, we have signed an EPP contract (now also called EPS – Equipment Protection Service) for five years. The Equipment Protection Plan includes regular inspections, as well as key service functions and spare parts”, Schön adds.
The first Nordberg® GP330™ cone crusher in Germany has proven its reliability at the BAG Rammelsbach stone quarry ever since 2016
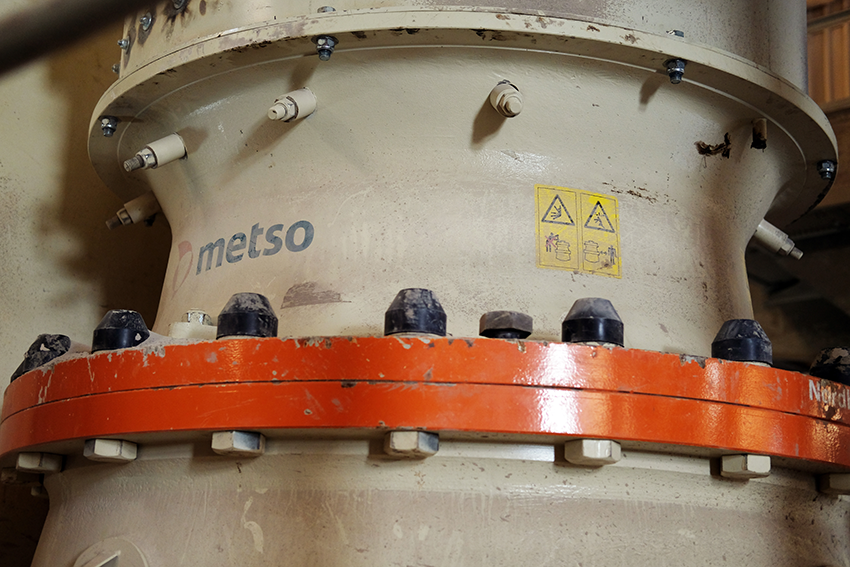

Old stone quarry with top-quality products
The history of the Rammelsbach stone quarry in Rhineland-Palatine goes back to the 1860s, when the excavation started. In the 1930s, Rammelsbach was considered to be the largest stone quarry in Europe.
Since 2001, they have been a part of Basalt-Actien-Gesellschaft (BAG), one of the largest rock producers in Europe. The company offers its customers a complete range of products, including railway ballast and different sized aggregates for asphalt, concrete and construction industries.
The feed material called microdiorite is quarried in Rammelsbach, and is also referred to as “Kuselit”, after the nearby city of Kusel. It's hard rock with a solid density of 2.68 t/m³ and is especially suited for producing top-quality railway ballast. For this reason, a large share of the total production is delivered to Deutsche Bahn AG, a German railway company.
The 150-year-old Rammelsbach quarry has reserve for the next 20 years, the very least.
It’s not just the quantity that counts in Rammelsbach, but rather the constantly top-notch quality. “We accurately document everything. Each produced piece of rock must comply with the top quality standards regarding size and shape, to name a few”, Schön stresses.

Nordberg GP330 – the new centerpiece of the whole facility
The extracted microdiorite is transported via dump truck to the gyratory primary crusher. Afterwards, the product is screened into three sizes: The 0-32mm material is separated from the rest of the feed, and 32-70mm and 70-240mm stored temporarily in silos and then transferred via feed conveyors to the Nordberg GP330 hydraulic cone crusher.
The GP330 produces well-shaped material with a size of 0-80mm at a constant throughput of 340 t/h for further processing. The cone crusher has Extra Coarse (EC) cavity profile, approximately 34mm closed side setting (CSS) and 32mm stroke length. Stroke can be adjusted by rotating the eccentric bushing inside the crusher, which is a distinct feature of all the Nordberg GP cone crushers. This allows the GP crushers to be adjusted to match every application's needs; for example to maximize capacity or to reduce the amount of the produced fines.

GP330 is also easily converted from secondary crushing stage to suit tertiary crushing by just changing out the manganese wear parts, giving it excellent versatility.
Microdiorite is very abrasive feed material, and for this reason the crusher wear parts need to be replaced after 1,900 operating hours or so. However, due to the high throughput and excellent degree of utilization, the specific costs of manganese wear parts are low. The bypass oil filter also saves costs, as it considerably extends the service life of the hydraulic and lubrication oil.
Read more on our product page.
