Dundee Precious Metals Inc. (DPM) is a Canadian-based, international gold mining company engaged in the exploration, development, mining and processing of precious metal properties. DPM’s current operations are in Namibia and Bulgaria, with exploration in Bulgaria, Ecuador and Serbia. Ada Tepe, commissioned in 2019, is the first greenfield mine in Bulgaria in the last 40 years. The Ada Tepe mining operation has open-pit mining, with some of the processes including crushing, milling, flotation, dewatering and filtering circuits. The tailings from the process plant are stored at an Integrated Mine Waste Facility (IMWF). The concept of the IMWF is to place thickened tailings into cells constructed from mine rock. Rehabilitation of the slopes is being performed during operation compared to conventional tailings. The mine produces high grade gold concentrate which is then transported for further treatment in a smelter.
Ada Tepe Mine achieves gold recovery milestones with Geminex™ digital twin
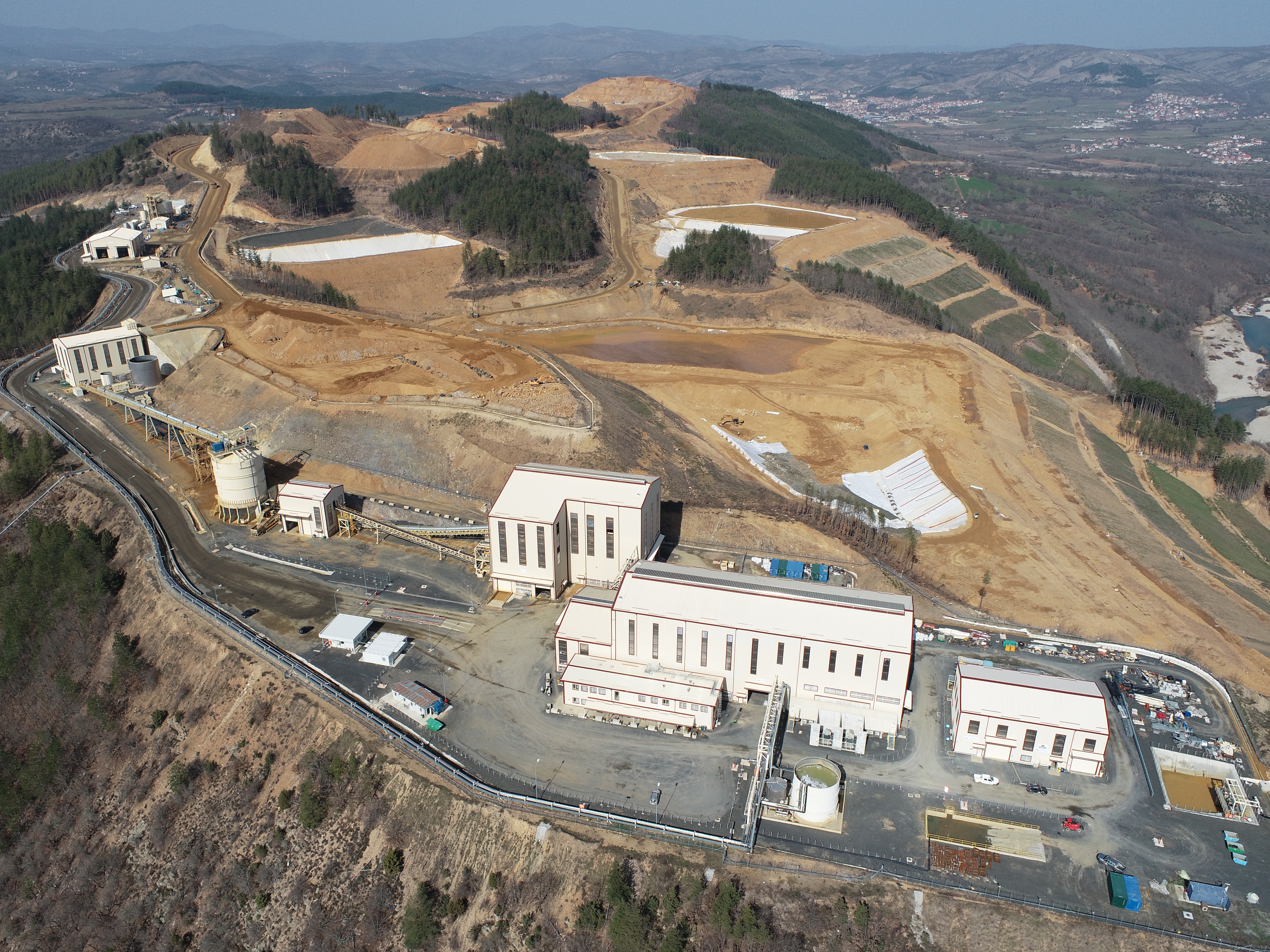
- Ada Tepe plant required enhanced process control and ability to make real-time adjustments to improve plant performance and increase gold recovery
- Metso Geminex™ digital twin which allowed to create a virtual representation of Ada Tepe’s mining and processing operations
- Digital twin provided a complete view of process status and identifies areas requiring corrective actions
- Increased confidence of process plant operators
- Accurate predictions of any proposed changes to the plant received
- Trial and error scenarios were tested and fully understood in simulation before implementing the changes in the live production environment
- Better understanding and management of the process contribute to reaching the production targets and higher gold recovery
- The simulation by the digital twin gives a complete view of process status, as well as visibility to areas where corrective actions are required
Next step towards optimization
At Ada Tepe plant process optimizers are used for optimal process control. A Model Predictive Control (MPC) based grinding optimizer covers the grinding circuit with SAGmill and Vertimill, and ensures consistent grind size for flotation feed, which is the key parameter for plant performance. The flotation circuit uses flotation optimizers for maximizing recovery and consistent process control. Optimizers in the dewatering section take care of turbidity of thickener overflow with optimal flocculant dosage and underflow density control that are critical for the IMWF feed.
The limits of targeted KPIs and input parameters of process optimizers can be adjusted by simulating the process within the digital twin by what-if scenarios. This process can be automated and linked to the process optimizers, which was a logical next step for Ada Tepe mine.
So as part of a larger digitalization project to employ model predictive process optimizers for process control, DPM investigated digital twin technologies. The process started by exploring how the digital twins are expected to add value, what it can do, and finally, what benefits are available with a digital twin in operation.
DPM found out that digital twin adds value by:
-
making operation systematic across working shifts
-
allowing faster reaction to issue to minimize impact of events where and when required
-
evaluating options for de-bottlenecking
-
eliminating unnecessary changes in the process
-
better understanding of process dynamics
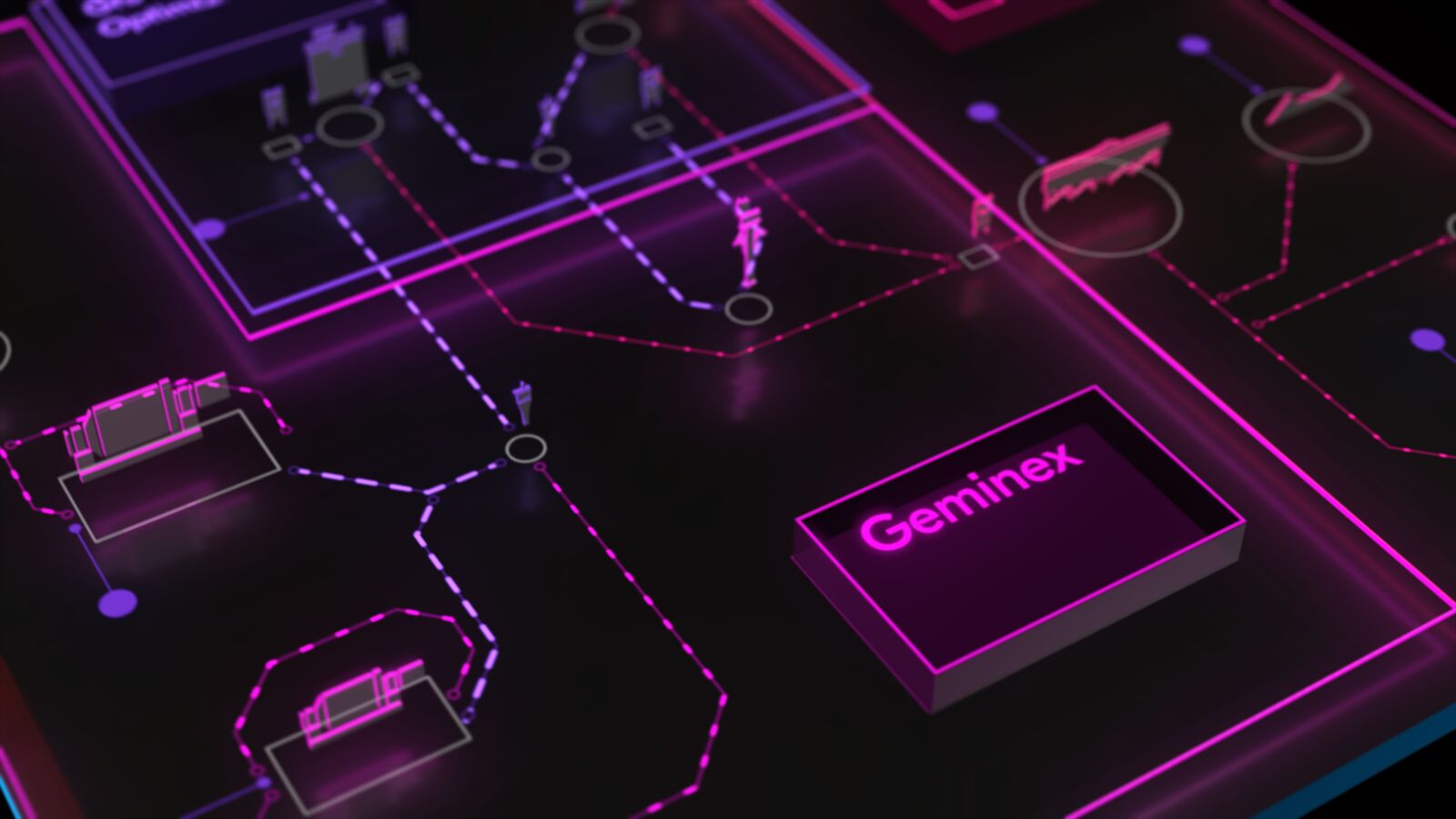
Meticulous project implementation
Metso assisted Ada Tepe through the intricate process of implementing the Geminex™ digital twin, offering invaluable expertise and support at every step. The project unfolded in three distinct phases, each carefully designed to bring the digital twin to life:
Phase 1: A static model of the flotation process was created with an actual process flowsheet.
Phase 2: The static process model was converted to a dynamic model with equipment hold-ups to allow for time dependent simulations.
Phase 3: The created digital twin simulation model was connected to live plant data for effective model adaptation.
Cybersecurity
Metso and Ada Tepe’s experts placed a strong emphasis on cybersecurity to protect sensitive data. This involved aligning the digital twin with corporate IT policies and practices, with the system running securely on Microsoft Azure cloud, providing scalability for complex simulations and a safe platform for maintenance and support. Metso also recognized the importance of user experience (UX/UI). By considering customer journey mappings, they tailored the digital twin’s interface to resonate with operators and plant metallurgists, making it more user-friendly and familiar.
Soft sensors
The digital twin introduced soft sensors – a novel feature not typically found through traditional means. These sensors allowed metallurgists and operators to gain valuable insights into the performance of individual process units and circuits. They provided critical information on aspects like mineral particle floatability, mineral content in different particle size fractions, and dynamic materials balance within the flotation circuit. The digital twin also integrated analytics tools to unearth meaningful relationships within historical process data and simulated information.
In addition to real time monitoring, the digital twin provides the metallurgists with an opportunity to test the outcomes of alternative processing parameters. The scenarios are built by scenario cards. With the scenario predictions the metallurgists can find optimal processing parameters for each shift to reflect the ore blend available.
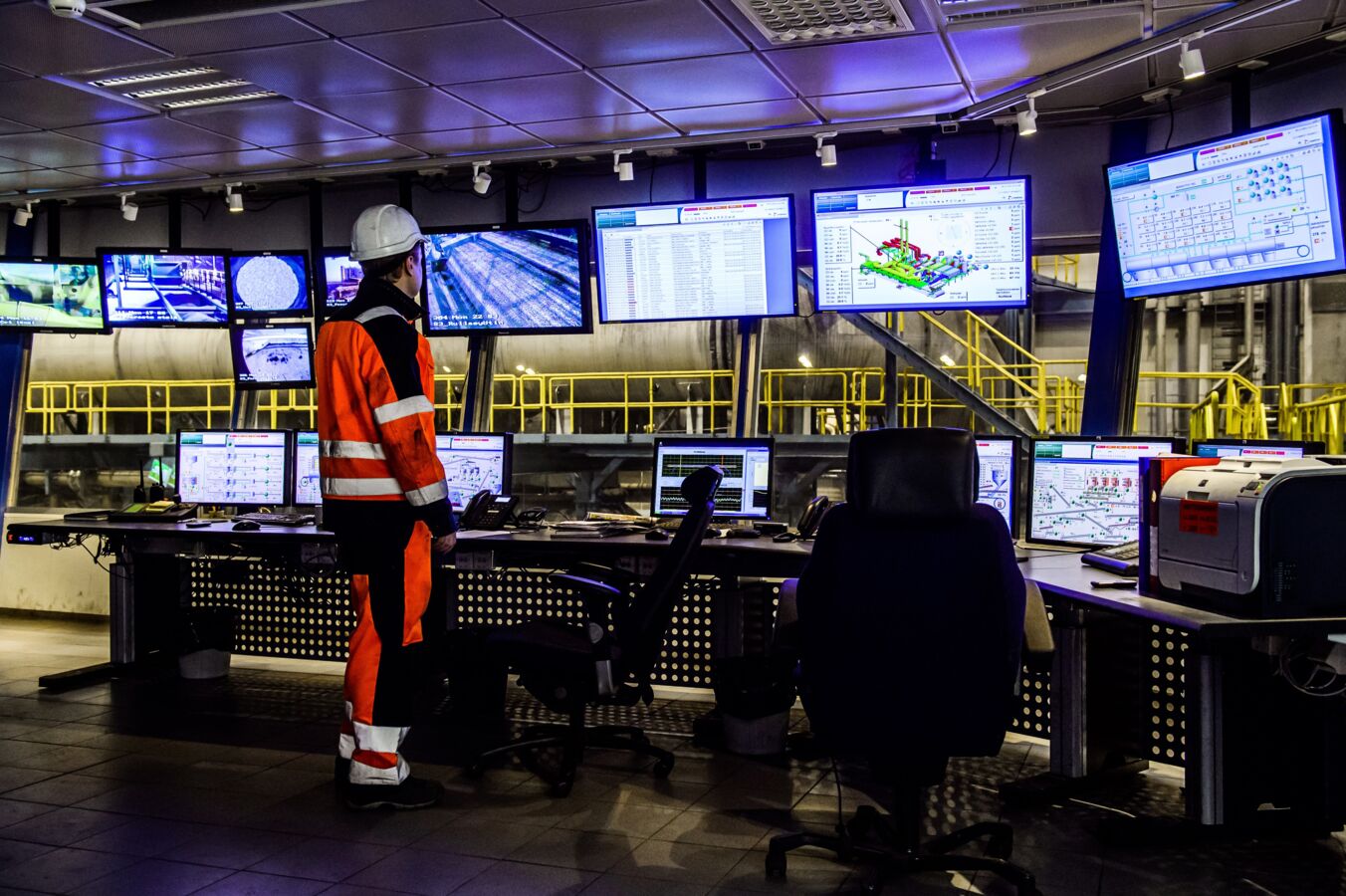
Unlocking multiple benefits of GeminexTM
Ada Tepe currently uses the digital twin for what-if scenario simulations at the beginning of every shift and makes the data available to operators for decision making. This allows the operators to learn how the key performance parameters will change when adjusting the flotation reagents, slurry levels of flotation cells or throughput with the existing ore feed. In addition, the operators can check the impact of other parameter settings with what-if simulations as needed.
The implemented digital twin helps increase the confidence of operators, as well as delivering assurance with any proposed changes to process parameters. Trial and error scenarios are tested and fully understood in simulation before implementation in the live production environment.
At Ada Tepe, one of the KPIs is compliance to predicted recovery generated by Recovery Model. The Recovery Model is a regression formula generated with past actual data, and it is used for production budgeting and forecasting. A positive trend on compliance to the Recovery Model could be observed from the chart after commissioning of the digital twin in the beginning of year 2022. This suggests better understanding of the process and implications of changes in processing parameters, which has contributed to reaching the production targets, and eventually higher gold recovery.
A vision for the future
Metallurgical digital twins hold immense potential for the mining industry. It enhances safety, increases production efficiency, boosts valuable mineral recovery, reduces energy consumption per ton of product and mitigates environmental impact. In a future marked by energy and water constraints and complex feed materials, the development of modern technologies will demand a high level of control and optimization. This is the promise that the metallurgical digital twin brings to the industry, shaping a future where responsible mining is the cornerstone of success.
This case study is an abbreviation of the paper “On-line digital twin for processing plant optimisation” (Moilanen et al) presented at the MetPlant 2023 conference in Adelaide, Australia.