The location of Nexa Resources in Três Marias (state of Minas Gerais) is one of the Brazilian multinational plants, focused on zinc production. The process involves a zinc hydrometallurgy, which means that this plant needs to transport pulp containing solids, often being extremely acidic and at high temperatures through hundreds of meters of pipelines. This transportation is done by centrifugal pumps and/or through positive displacement pumps which, unless exceptions, should only be paralyzed under controlled conditions. However, this was not what happened at the plant at the end of 2018. The production was partially interrupted, on average every 30 days, due to breakage of pump bearing and shaft, at a flow rate of 280 m3/.
Nexa installs Metso Outotec pump in Três Marias
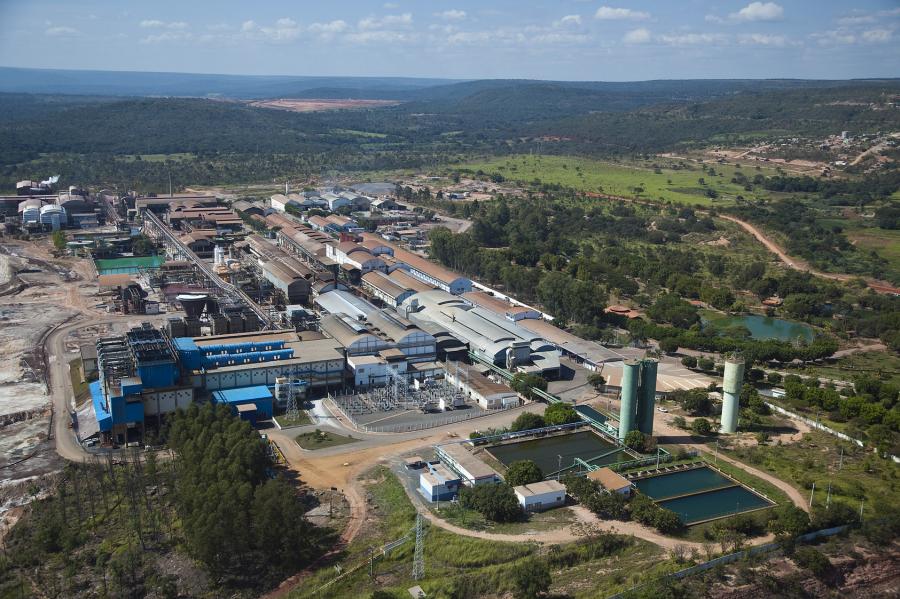
The constant failure had two consequences for Nexa: it affected the hydrometallurgical process, thus compromising the production, and had turned out to be an occurrence of corrective maintenance, when it is best that these kind of problems do not happen or, at least, are identified in advance, allowing for a correction during the programmed downtime. Being an equipment of earlier generation, the pump also was equipped with heavier components than the more recent pumps and furthermore had a higher amount of components. In short, service was more complicated than the maintenance carried out for more recent pump models.
The identification of the problems was made by the Nexa team, headed by engineer Jean Deybe Pereira do Nascimento, responsible for the initiative to test another equipment with similar flow rate and equipped with a shorter shaft and higher mechanic resistance than the problematic pump. “We worked together in order to identify the most adequate model, including the material specification to deal with the corrosiveness of the transported pulp”, explained Nascimento.
Shaft of new pump is shorter and made of higher resistance steel
After being contacted by Nexa, Metso Outotec started by evaluating the operational conditions of the pump. The idea behind this study was to eliminate the operation itself as the source for failure and confirm the problem in the equipment, which was detected. The source being confirmed - a greater deflection of the pump shaft - Metso Outotec suggested to substitute the equipment by a modern model, of advanced design, and which would occupy less space in the plant. The easier assembly and disassembly was also considered. Besides eliminating the problem, the new pump achieved a flow rate of 300 m3/h, surpassing the capacity of the competitor´s model, which was used to that date.
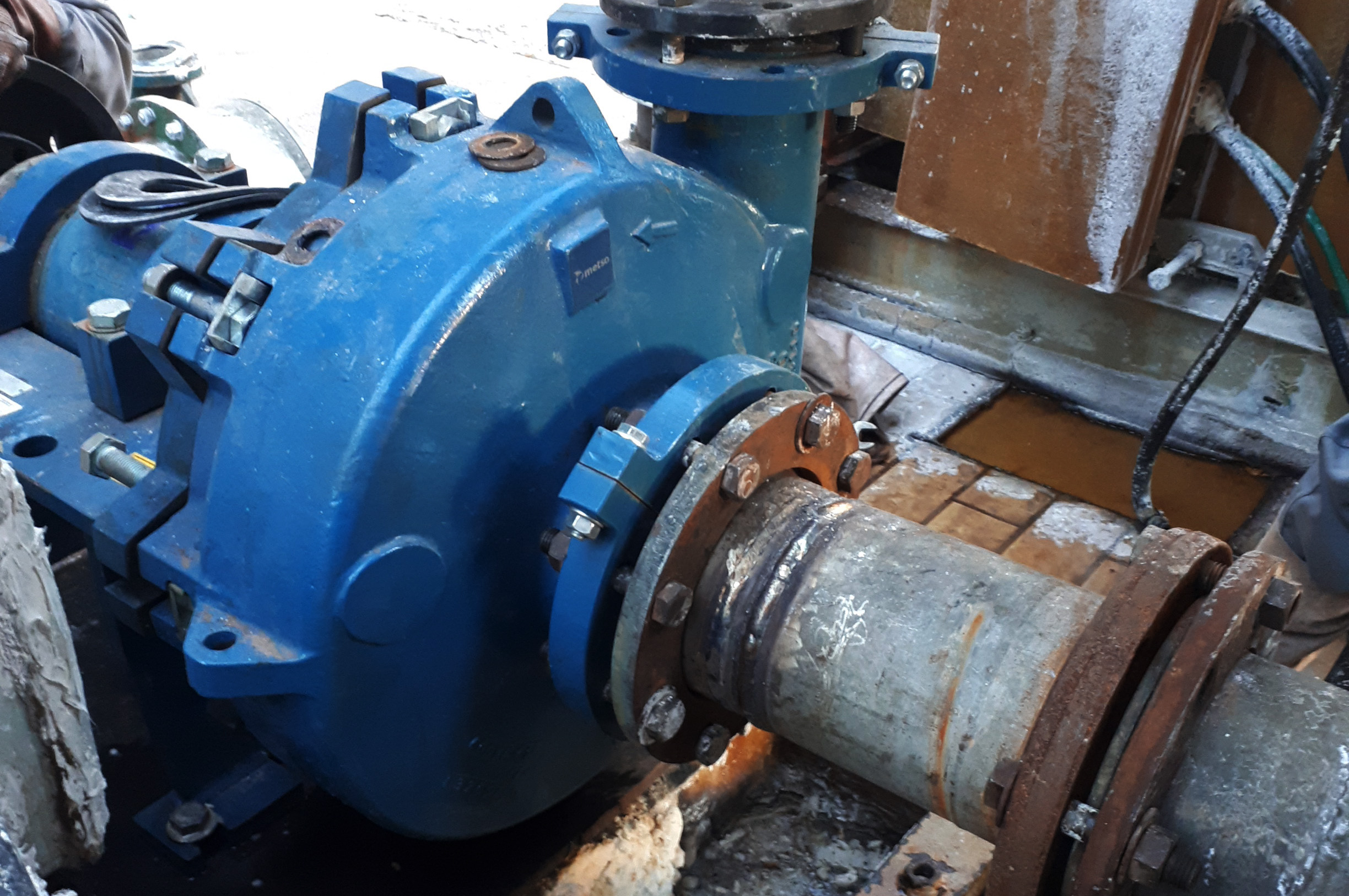
With this positive result, Nexa adopted the same pump model for other areas of the plant - which has a fleet of about 600 products of this type. The new products, however, followed specifications developed by Metso Outotec during test phase, meeting all technical requirements specified by Nascimento. “Metso Outotec was structured for casting of ideal pumps for abrasive pulp. Currently there are seven of them operating in areas like repulping and in the thickener”, he explains. In addition, Nascimento pointed out that testing and the usage of the equipment in Três Marias resulted in the qualification of the technology for other Nexa locations.
Eduardo Orsi, Sales and Application Manager for pumps at Metso Outotec emphasized that the on-site consulting at Nexa allowed for selection of the pump model in accordance to the conditions indicated by the company and considering the corrosion, erosion and thermal characteristics of the conveyed fluid, amongst others. “As the previously used pump was equipped with a longer shaft balancing between rotor and bearing, the shaft was subject to deflection, causing it´s constant breakage. As to the HM 150, our pump model, the balancing shaft is shorter, causing less deflection and thus reducing substantially the risk of a breakage”, he explains. According to a joint technical study, the shaft breakages occurred next to the fastening thread of the rotor, confirming the main source of the problem.
Metso Outotec´s HM 150 operates at full flow rate and without shaft breakages
“The engineering approach worked out together with Nexa was not limited to selecting a more appropriate model in terms of mechanical structure. We also chose to apply a special metallurgy to the shaft, whose mechanical properties are superior to the existing pump”, describes Orsi. The HM 150 model acquired by the metal company was also manufactured with a different constructive material, abandoning the traditional alloy (high chrome) and adopting the alloy CD4MCuN, indicated by Nexa, in order to meet the characteristics of the conveyed pulp in the zinc concentration plants.
The HM 150 also features a user-friendly design, which allows for easy routine servicing operations. It has fewer components than the prior model and its features facilitate interventions. The equipment offers low cost and spare parts which follow this trend.
“Pumps are an essential asset for our process, which is basically hydric, consisting in transport fluids from one point to another”, explains Nascimento. “We operate with small and medium size equipment, but they convey acid and hot pulp and solutions, in other words, they operate under extreme conditions”, he complements. “The assistance given by Metso Outotec surprised us, as did the delivery times and the quality assurance”, he concludes.
About Nexa
Nexa Resources is one of the worldwide leading zinc mining companies, who also produces copper and lead. The company has been operating over 60 years in the mining and metallurgic sectors, with operations located in Brazil and Peru as well as offices in Luxembourg and the US, delivering its products to all other continents in the world. Nexa´s employees work every day focused on building the future mining, to be increasingly sustainable, innovative and with best practices with regard to safety, respect for people and environment. With shares are traded at stock exchanges in New York and Toronto since 2017, the company is also controlling shareholder of Votorantim S.A.
For more information about Nexa, visit www.nexaresources.com