A little over a million metric tons of feed goes through Metso’s second largest GP series crusher at the mine each year. More than half of this volume is refined into raw material for the manufacture of cement, and the rest is turned into other limestone products.
Nordkalk’s new GP500S secondary crusher doubles the crushing ratio and facilitates process adjustability

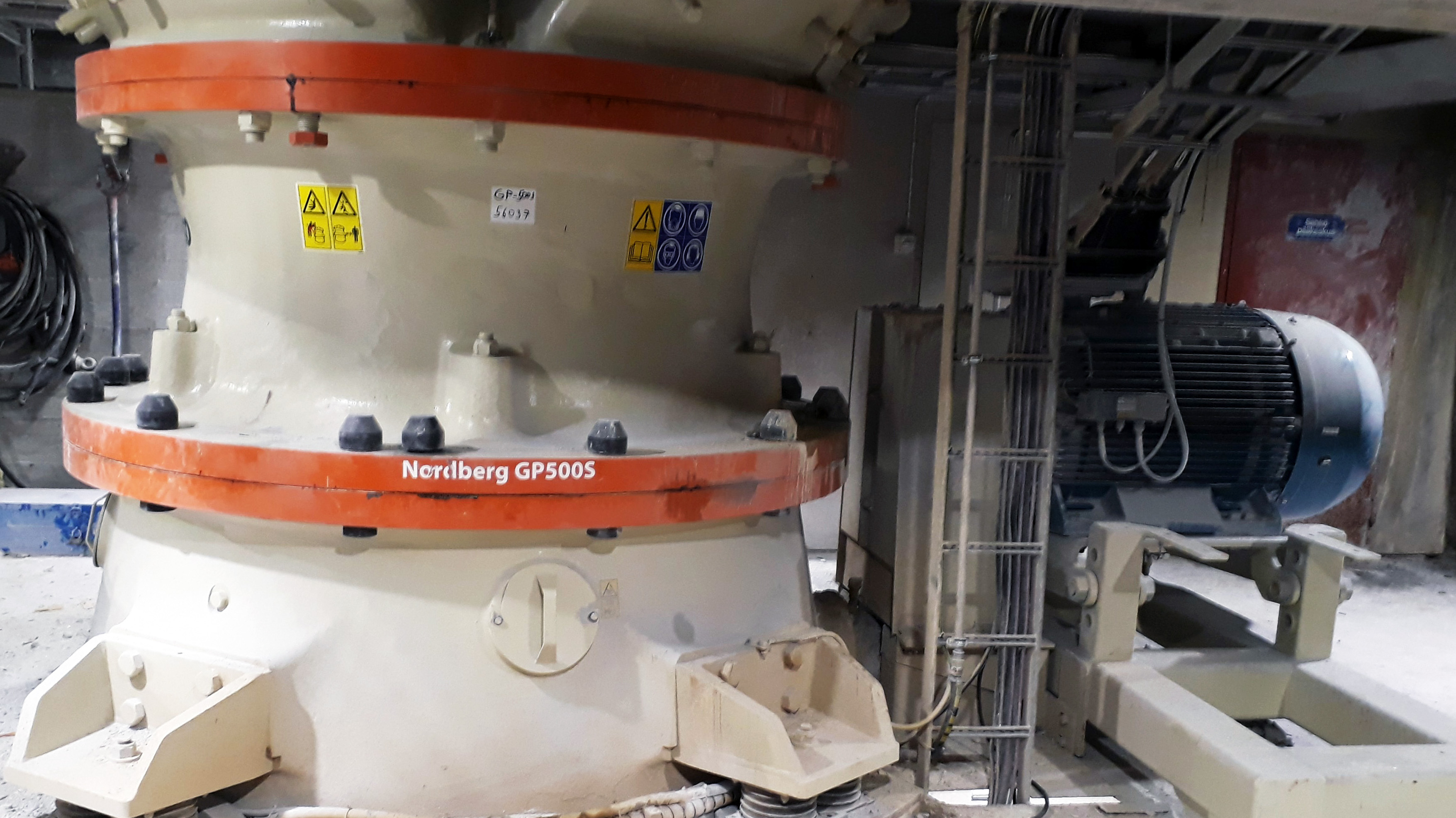
A curiosity produced by the Lappeenranta mine is wollastonite, which, in addition to Nordkalk, is only produced by two other mines in the EU and in the United States and China.
“Lighter fine crushing, enough capacity for expansions”
Petri Repo, Maintenance Manager, Mika Pohjonen, who is in charge of mechanical design in the project, and Pertti Vasara, who is in charge of the mine’s mechanical maintenance, are happily having coffee in the tidy staffroom of the Nordkalk Lappeenranta mine, located 50 meters into the rock. The secondary crusher replacement operation has been successfully completed.
“The acquisition of the GP500S and its installation by Metso during the July shutdown actually went exceptionally smoothly. Even in our cramped underground facilities, the installation was completed exactly on schedule, and the promised crusher capacity has been achieved,” Petri Repo sums up the project.
“Compared with the product size of 80 mm produced by our old secondary crusher from Svedala, which was installed in the 1960s, the crushing ratio of the GP500S is better by half. This means that we can now feed material of some 40 mm into our fine crusher, which clearly lightens the rest of the process.”
“The larger gap size also reduces the risk of blockages in the crusher. In addition, we can use the modern IC50C process automation of the GP500S to adjust the crusher much more accurately than before. This is important, as we process a variety of minerals with very different characteristics,” Petri Repo adds.
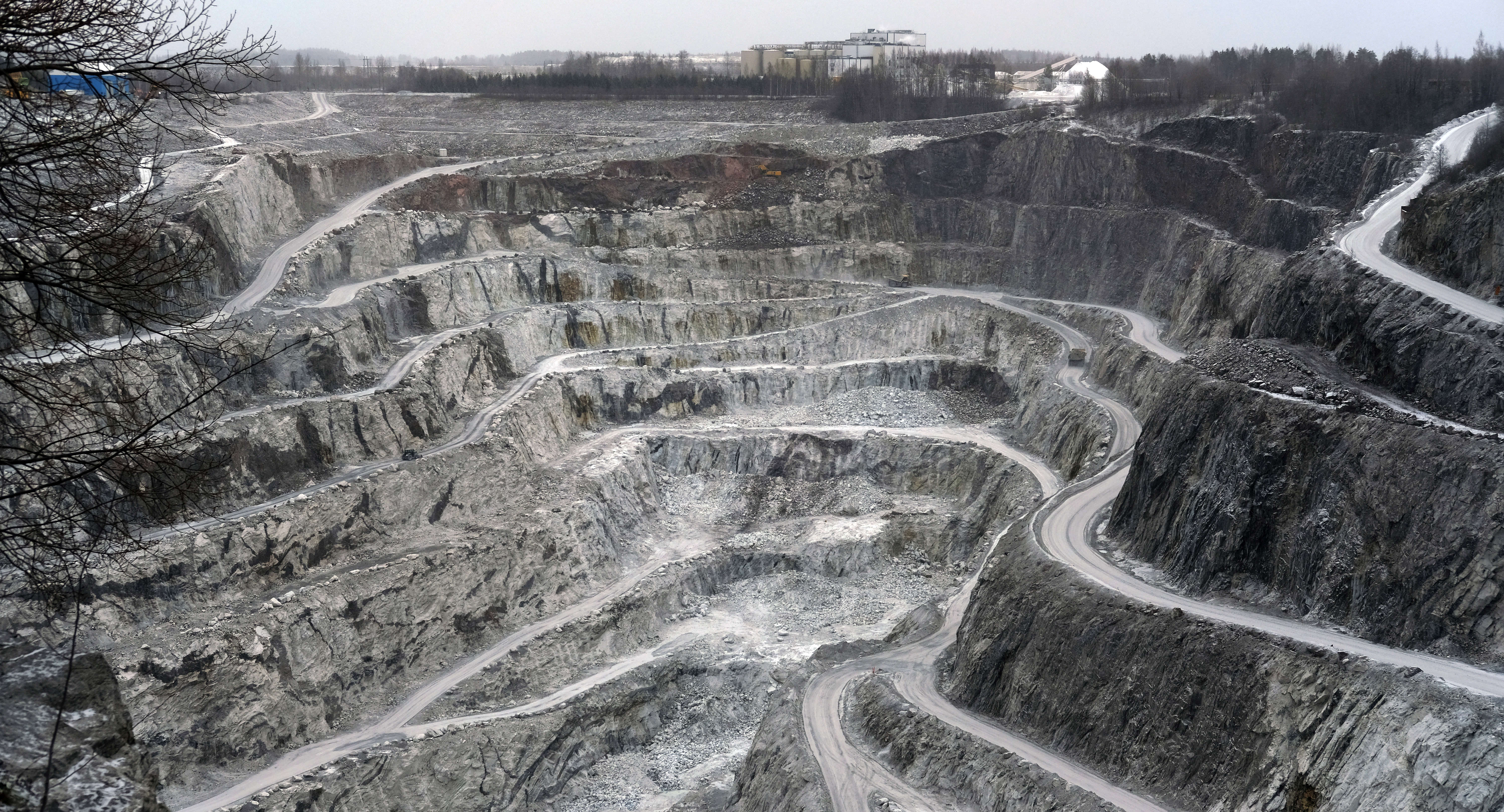
Enough capacity to increase production volume
At present, the feed of 0–1,000 mm from the 165-meter deep open-pit mine in Lappeenranta is transported by truck to a Blake 17 jaw crusher in the underground crushing facility. After primary crushing and screening, unwanted black rocks are removed from the process with an advanced computer vision system and compressed air.
The new GP500S receives feed of less than 200 mm, which is crushed to 38–45 mm before further crushing by the BMK7. After crushing, the material is taken to silos or storage piles, from where the different types of material are supplied to a cement mill or one of two concentration plants.
“At present, the capacity of our crushing process is some 400 metric tons. The new GP500S will allow us to increase the capacity in future if we decide to renovate other parts of the rock line,” Petri Repo says.
At the Nordkalk mine, wear parts of the secondary crusher last for approximately 18 months in production operation, because the only wearing minerals at the mine are black stone and wollastonite. After three months of continuous crushing, only the surface roughness has been lost from the mantles and cone of the new GP500S.
120 years of profitable operations
Nordkalk, part of the Rettig Group, produces more than 13 million metric tons of dehydrated lime, hydrated lime, ground limestone, calcite, paper pigments, and wollastonite at a total of 22 mines and open-pit mines in Europe. Most of the products are used in the paper and pulp industry, steel industry, chemical industry, and agriculture.
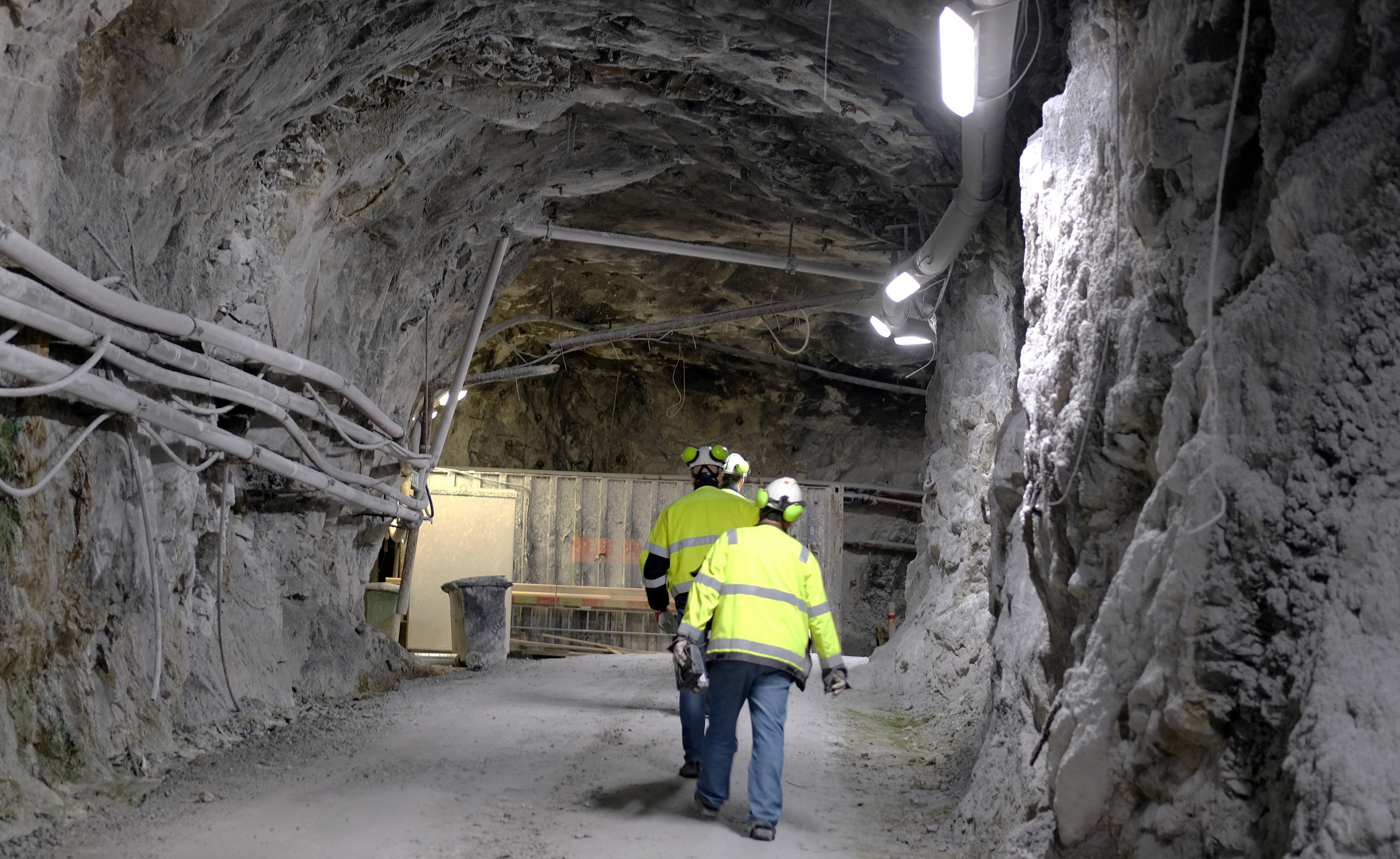
With its net sales of a little over €300 million and some 1,000 employees, Nordkalk is a special company: it has remained profitable throughout its long history.
The open-pit mine in Lappeenranta will be widened in the next few years to allow for a deeper embankment.