For the past eight years, the mine has collaborated with Metso to optimize the wear parts of the primary gyratory crusher, which has boosted production: the primary crushing capacity has increased significantly, and synchronizing the shutdowns has resulted in five more days of uptime per year.
Continuous wear part optimization boosts nickel production at the Terrafame mine
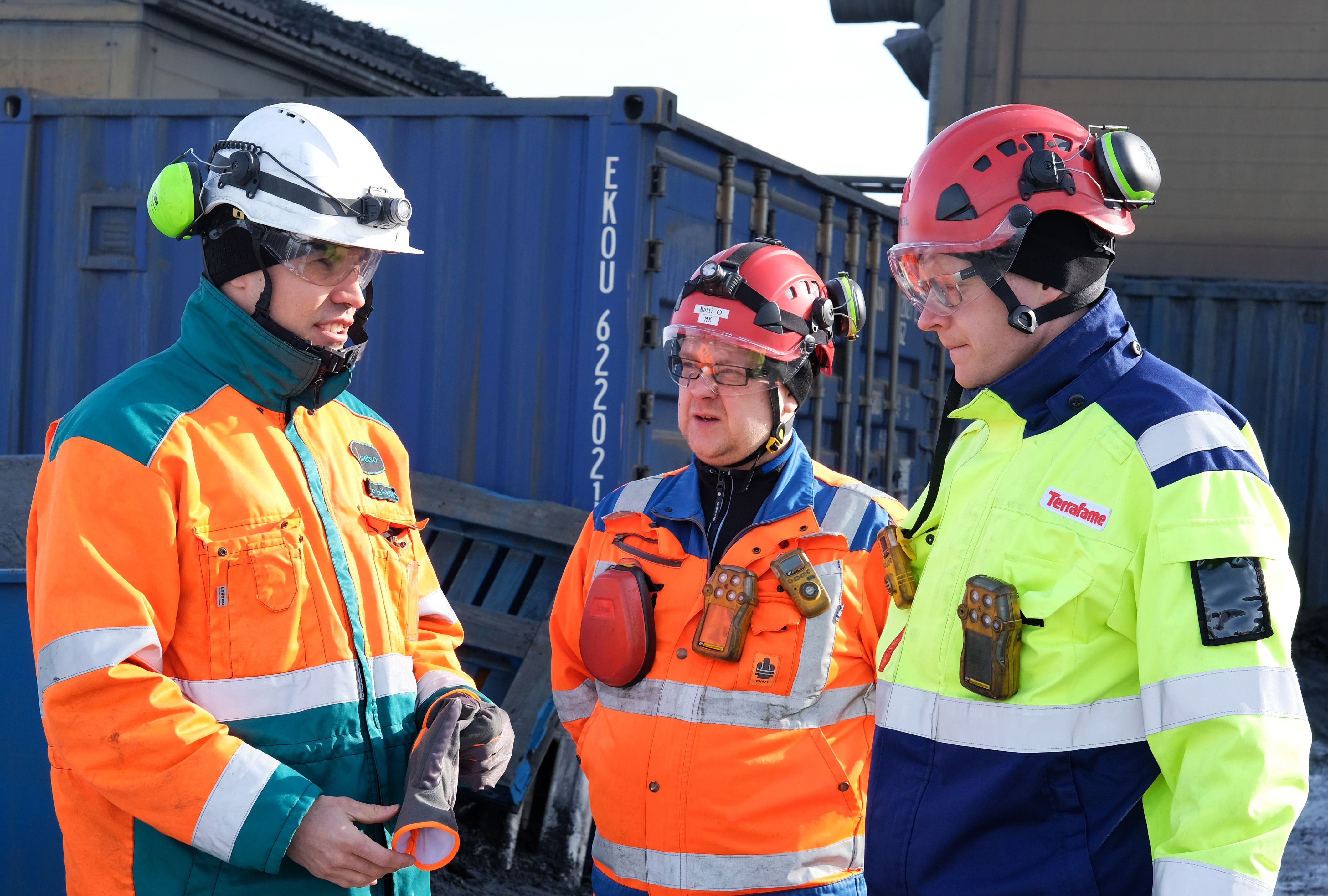
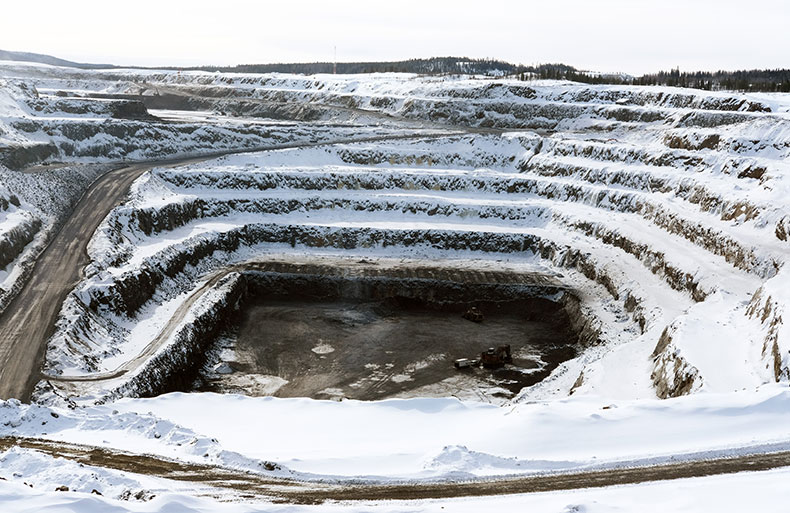
The first step of the collaboration in 2010 was to solve the challenges that the slippery, graphite-rich ore was causing for the primary crusher by redesigning the chamber profile. This bumped the capacity of the critical primary crusher to the desired 3500 tonnes per hour.
The next target, two years later, was to extend the wear life of the primary gyratory wear parts by optimizing the materials used. White iron was chosen for the two lowest concave tiers, and the mantle was made of a more ductile, high-grade manganese steel.
A five-day increase in annual uptime was now possible, as the longer lifetime of the primary crusher wear parts allows them to be changed out at the same time that the massive, mobile stacker used at the leaching heap is turned.
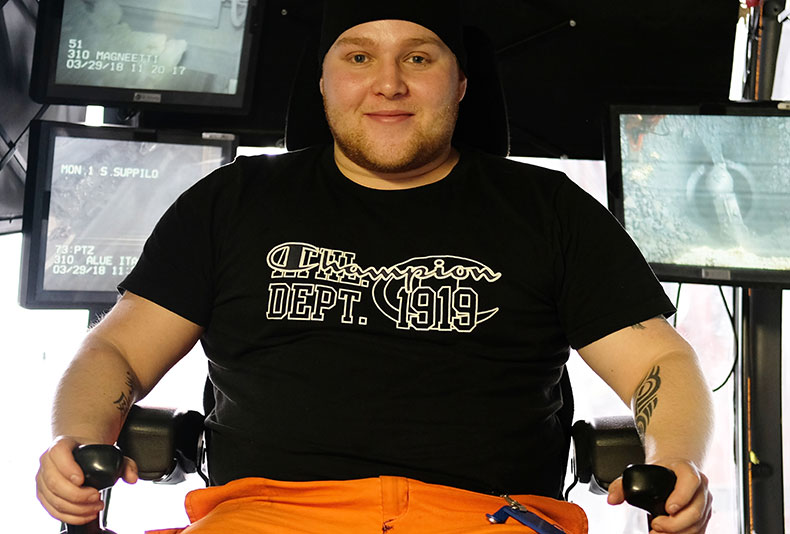
Multiplying the wear life of the mantle and the concave segments
Jarkko Kettukangas, Department Manager of Materials Handling at Terrafame, has some impressive figures to share regarding the wear-life improvements of the primary gyratory crusher’s wear parts.
“The development of the primary gyratory wear parts together with Metso has been outstanding. The wear life of the concave segments has more than doubled, from approximately 5 million tonnes gradually to the current 14 million tonnes. At the same time, the wear life of the mantle has improved significantly,” Kettukangas lists.
”We will continue the close collaboration. The next step is to further extend mantle wear life with new material options. The target is to use only three mantles per concave cycle instead of the current four.”
According to Jarkko Kettukangas, the redesign of the chamber profile together with blasting optimization now enable an hourly primary crushing capacity of 4000 tonnes.
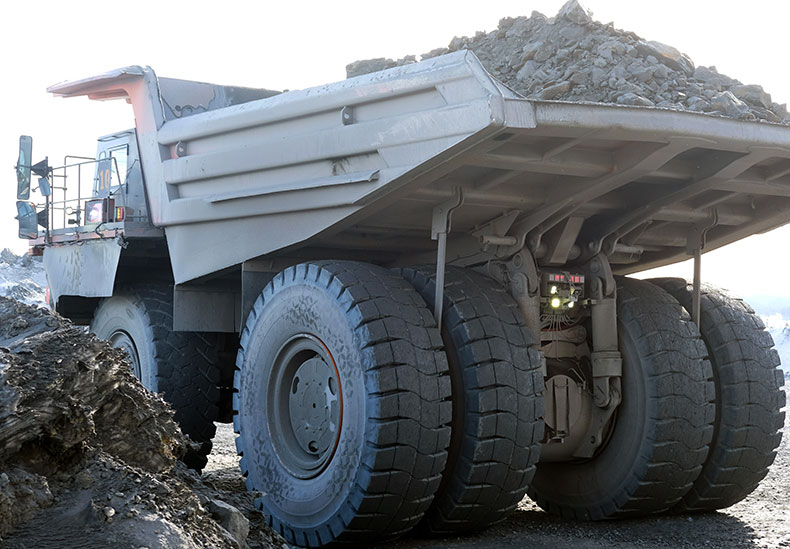
“Better throughput in the primary crushing stage gives some leeway in our daily work, because there’s more time left for maintenance. The primary crusher feed is finer than before, which means that we have what it takes to increase the crushing volume even further.”
Optimization software and material options play an essential role
The man behind the design of Terrafame’s 60-89 primary gyratory crusher’s wear parts is Metso’s wear part expert Mikko Malkamäki.
Metso’s proprietary chamber simulation software combined with decades of on-site experience are the key elements of successful chamber design.
“The capacity challenge caused by the sliding of the slippery nickel ore was solved by tightening the nip angle on top of the chamber by several degrees. At the same time, we reduced the feed opening to 945 millimeters and optimized the nip angle in the whole crushing area,” Mikko Malkamäki explains.
The right materials were chosen from Metso’s selection of alloys and composite materials.
“White iron turned out to be the most durable option for the two lowest concave tiers, the area most subject to wear. In the mantle, we have managed to extend the wear life with ductile, high-manganese steel, vertical grooving as well as by fine-tuning the material thickness,” he adds.
Towards positive results
Terrafame Oy is owned by the Finnish state, Trafigura and Sampo. The company gets its name from the “starving land” whose 0.26% nickel content it is now utilizing. In a short period of time, the mine has managed to work wonders by doubling both its turnover and metal production.
In 2017, nearly 21 000 tonnes of nickel, over 47 000 tonnes of zinc, as well as copper and cobalt, were extracted from the ore through bioheapleaching, a method which utilizes nature’s own bacteria. The 650 employees of the mine and the 630 subcontractors are hugely significant to the whole Kainuu region.
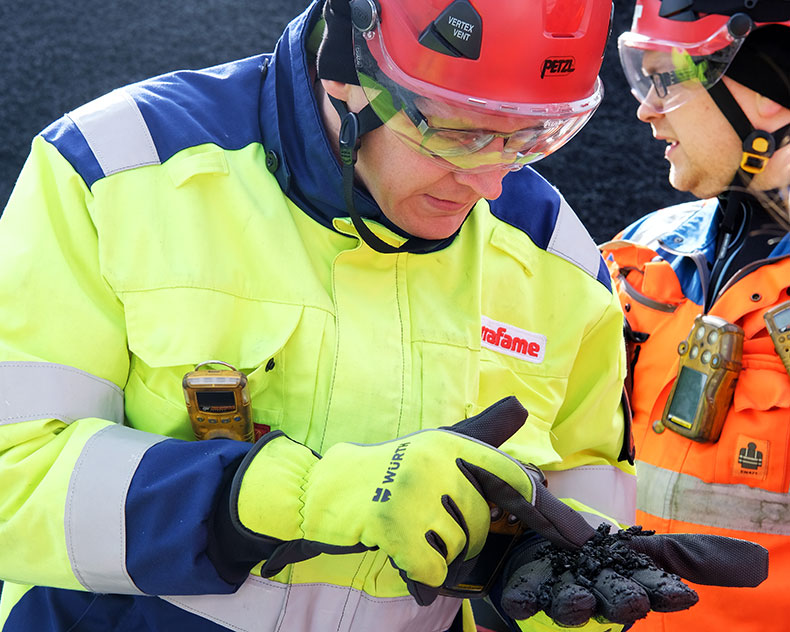
Jarkko Kettukangas ends his presentation about the mine with a slide that highlights Terrafame’s goal to turn the entire business profitable during this year. On site, one can truly sense the confidence in the work and in the future. The company is planning to set up a new plant in the mine area for the production of battery grade chemicals.