Case study: Enhanced efficiency with Nordberg® HP350e™
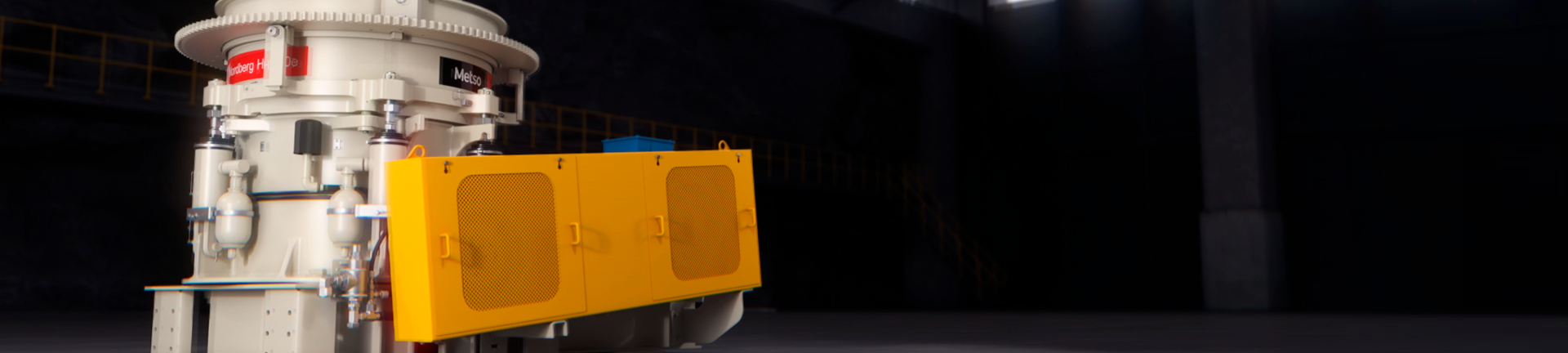
The new Nordberg® HP350e™ cone crusher provides better performance and uptime
in a more sustainable way. It offers enhanced performance, easier and safer
maintenance, and a series of other improvements, making it the perfect choice for
aggregate and mining operations.
- New enhanced kinematics and more efficient chambers.
- Up to +10% performance in Secondary and Tertiary application (compared to HP300).
- +10% more head motion.
- +14% more power (in kW) and +17% more power (in HP).
- +20% more force.
- No-backing liners for quick, easier and safer liner change.
- Head anti-spin brake extends liner wear life.
- Enhanced tramp release cylinder mounting.
- New feed cone lifting tool, for safe lifting and handling.
- Three alternative kinematics to choose from.
- Alternative speeds.
- Enhanced chamber designs and application specific chambers.
- Exceptionally wide chamber offering.

Enhanced performance
Evolution in performance is achieved by four factors: kinematics, chambers, release force and power rating. New HP350e crusher’s performance is up to +10% (compared to traditional HP300 crusher) when used in secondary application and in tertiary application.
Tune the HP350e crusher into the wanted application by choosing the optimal kinematics. There are three alternative kinematics to choose from.
- Enhanced kinematics for maximum performance in terms of capacity and reduction.
- Classic HP300 kinematics for conventional HP300 performance. This is to reach the same performance level as before with the HP300 crusher. When aiming at exactly to the same performance as with HP300 before, in terms of throughput and reduction, and when maximizing part similarity in the machine.
- Reduced stroke for reduced throughput. To be used when further limiting throughput for rest of the circuit, when tuning the crusher into a specific application, or when limiting power and force.
Improved uptime and serviceability
HP350e cone crushers are fitted originally with no-backing manganese (mantle and bowl liner). This saves time in liner replacement as no time is needed for backing compound solidification.
Logistics is easier as there is no need to source, store and transport backing compound.
Liner installation process becomes much safer as there is no need to handle, mix and pour the backing material. Solution is environmentally friendly as backing material is not needed.
Specific feed cone lifting tool provides further safety improvement, it is designed specifically for safe lifting and handling of the feed cone. Further developed tramp release cylinders are made easier to remove and re-install for easier service and maintenance of the equipment.
Extended liner lifetime thanks to the head anti spin brake, which slows down head spin on idle. Optional ring bounce monitoring enhances machine protection.
Great parts compatibility between crusher generations
Majority of the spare and wear parts of the new HP350e and the HP300 cone crusher are compatible enabling economical, operational and environmental benefits for mixed fleet operations. With the bowl and head upgrade kit, the new no-backing liners can be installed in the HP300 cone crusher. Classic HP300 liners with backing material can be used in the HP350e crushers alternatively, too.


Wider application coverage
New application specific chambers:
- Coarse chambers EC (Extra Coarse) and C (Coarse) for the most efficient secondary crushing
- Fine end chambers for tertiary and fine crushing
- F-NF (Narrow Fraction) to maximize yield of typical aggregates fractions (for example 5-8mm / ¼” x 3/16”, 8-11 mm / ½” x ¼”)
- F-Sand chamber for specific high quality sand production
Technical specifications
Metric | Imperial | |
---|---|---|
Basic crusher weight * | 16,000 kg | 35,200 lbs |
Complete crusher weight ** | 18,300 kg | 40,300 lbs |
Maximum power | 250 kW | 350 HP |
Head diameter | 1120 mm | 44” |
Stroke options | 93 mm / 84 mm / 69 mm | 3-11/16” / 3-5/16” / 2-11/16” |
Number of chambers*** | 10 | 10 |
Capacity up to | 485 mtph | 535 stph |
* Bare crusher weight ** Crusher weight with options *** Additional offering: optional liners range for use with backing material. Different alloy alternatives. |
Spares, wears & services
Contact local sales experts
Select your industry to open the form.
Your information is safe. Check our privacy notice for more details.
Thank you!
We will shortly contact you. You can send a new inquiry again after 15 minutes.