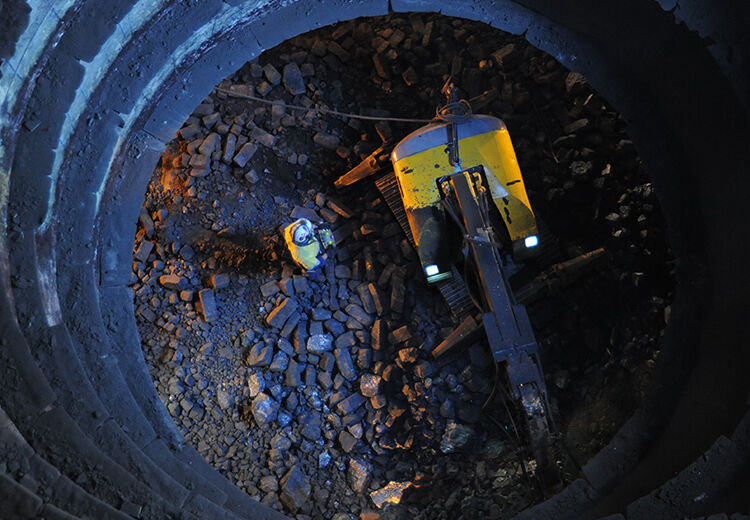
How can Metso help?
Improve safety
Our special line of equipment keeps crews safe.
Increase uptime
Keep your system running with regular inspection and maintenance.
Minimize shutdown time
Our lance equipment can cut slag up to 5x faster than others.
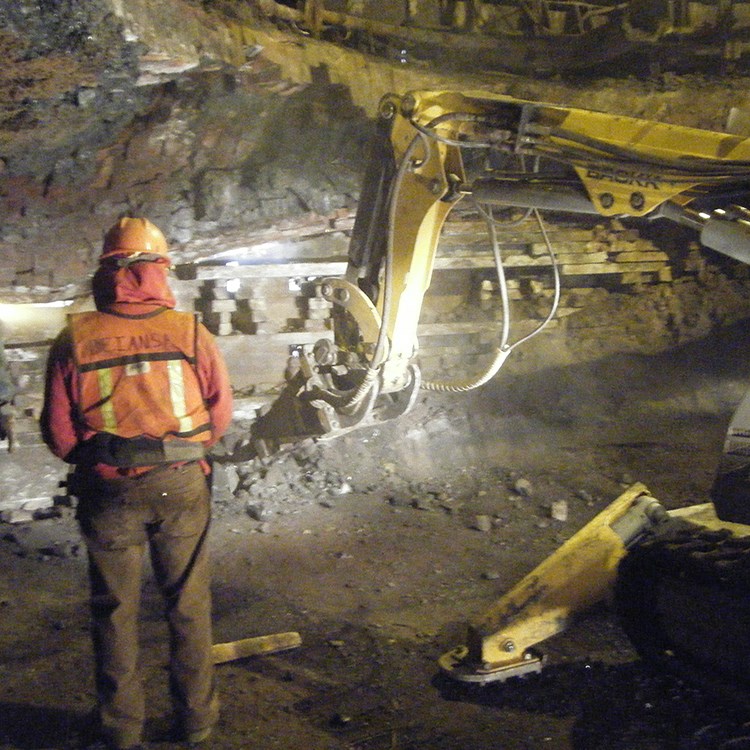
Metso has been performing demolition work all over the world for the past 35 years, with references from over a thousand projects. Metso’s top demolition experts each have over 25 years of experience in furnace demolition. Metso has experience with the following furnace types and metals:
- Flash furnaces – Ni, Cu
- Electric furnaces – round, six-in-line – Ni, Pt, Fe-alloys, Ti-O₂, slag
- Noranda reactors – Cu
- Peirce-Smith converters – Cu, Ni
- TSL furnaces – Ausmelt, Isasmelt – Cu, Pb, Sn, e-scrap
- Kivcet furnaces – Cu, Zinc, Pb
- Anode furnaces – Cu
- Rotary holding furnaces - Cu
- Shaft furnaces
- Pelletizing line furnaces – Fe
- Blast furnaces – Fe
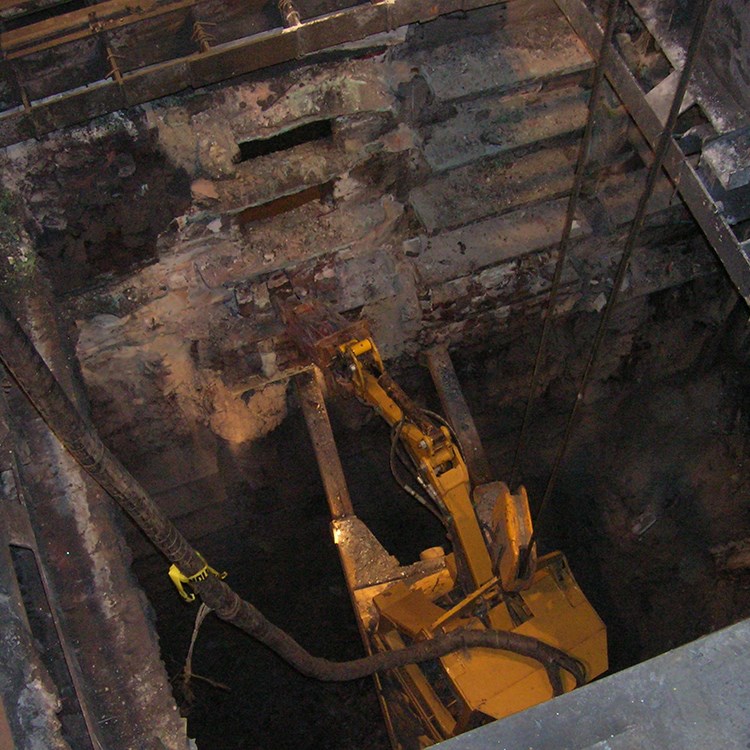