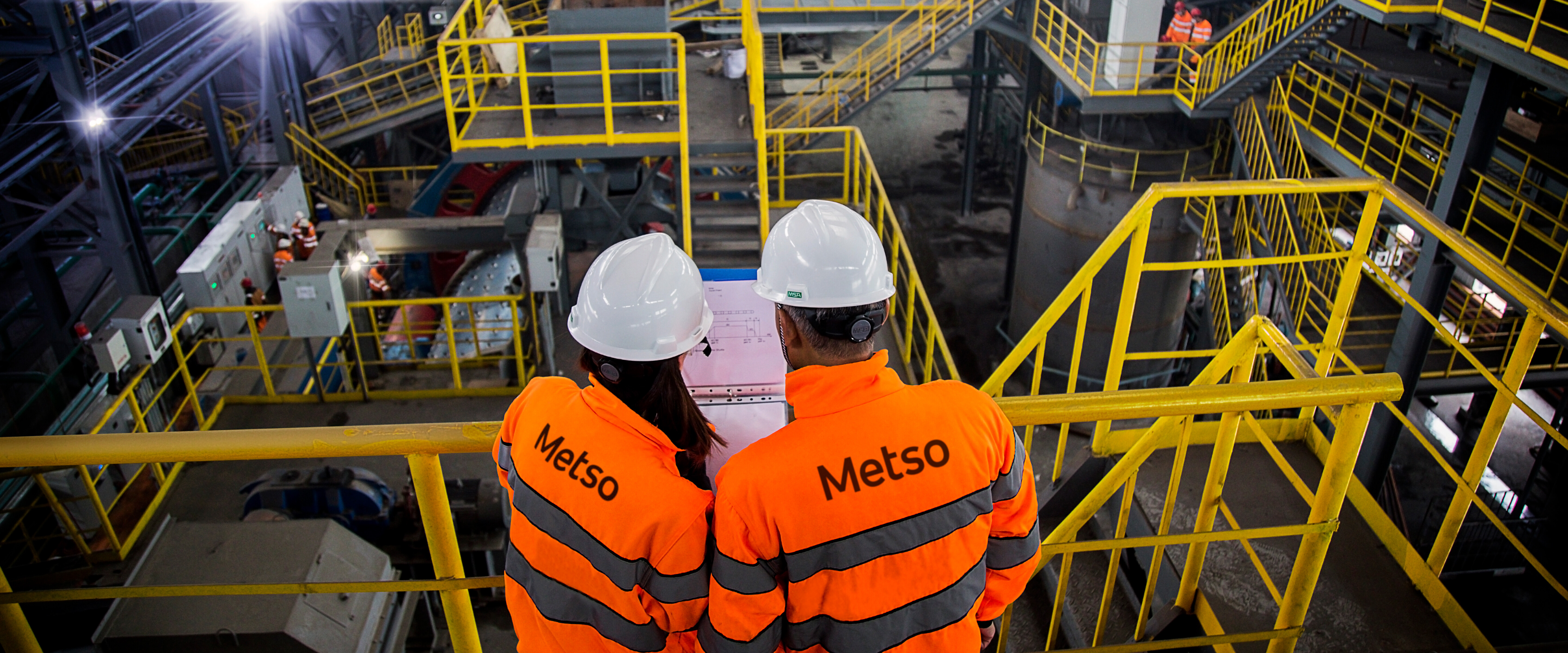
Identifying problems before they escalate ensures higher equipment availability
Minimize the risks associated with operating faulty equipment to ensure higher safety
Undetected issues can lead to breakdowns and unplanned service work, significantly increasing repair costs and production losses or quality.
Our specialists can recommend service agreements and spare parts along with clear and concise reporting
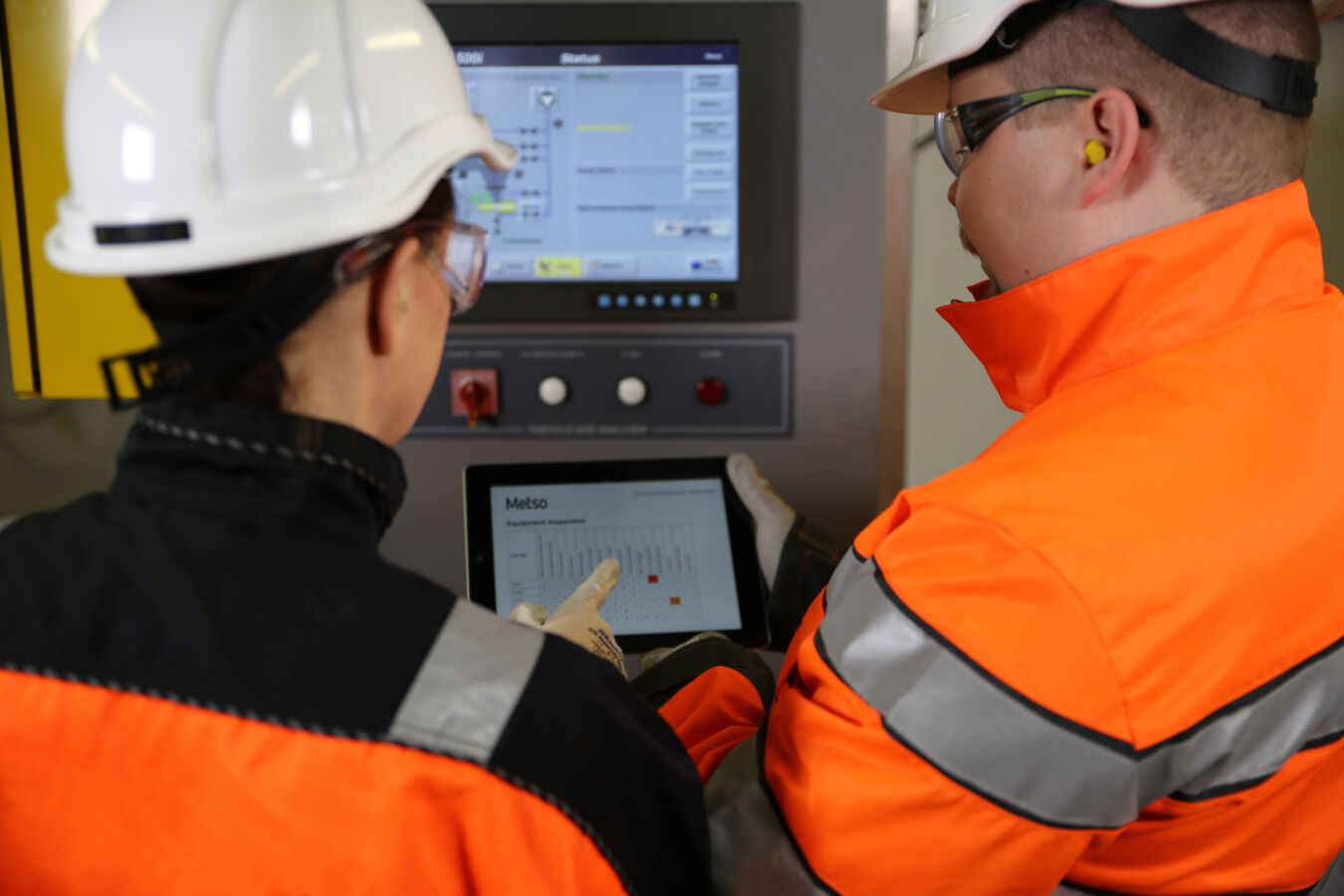
Benefits
- Reduced downtime
- Extended sampler lifetime
- Increased reliability
- Improved safety
- Process quality due to accurate sampling (needed for analyzers to work)
- Better visibility of maintenance requirements
Features
- Faster, easier inspections mean you get recommendations you can quickly act on
- Reports are clear, thorough and easy to share with colleagues
- Benchmark your samplers and identify trends based on current and historical data
- Comprehensive data gathering improves your decision-making
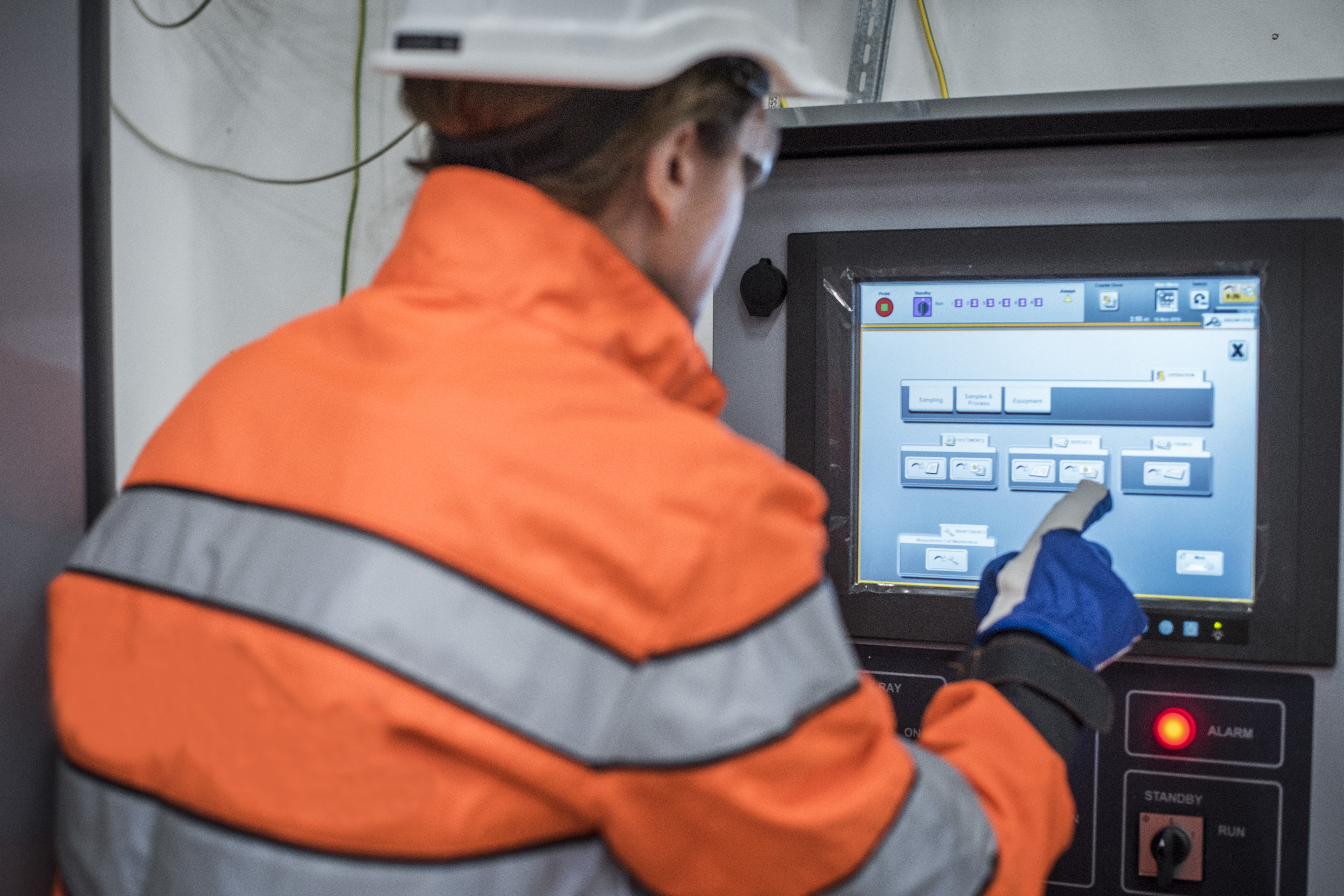
A quick way to understand your sampler overall condition during operation.
Downtime required: No downtime, duration one day for 10-15 samplers
Inspection frequency: 1-2 times per year
Inspection offering:
• OEM visual inspection of the sampler during operation
• Catch safety hazards, overall sampling results, maintenance intervals and leakages
• Historical data helps predict sampler component performance over time
• Detailed future inspections recommended if needed
Maximized availability through detailed inspection.
Downtime required: 3 days+
Inspection frequency: 1-3 years interval
Inspection offering:
• OEM inspection with guards and covers removed
• Additional tests, measurements and services
• Mechanical adjustments as required
